Electroplating solution and preparation method thereof
An electroplating solution and electroplating tank technology, applied in the field of electroplating solution and its preparation, can solve the problems affecting the composition ratio of the coating layer, uneven color and ash, rough surface, etc., and achieve the effect of qualified product quality, no roughness, and smooth surface.
- Summary
- Abstract
- Description
- Claims
- Application Information
AI Technical Summary
Problems solved by technology
Method used
Examples
Embodiment 1
[0022] A kind of preparation method that is applicable to above-mentioned electroplating liquid, prepares according to the following steps:
[0023] a. Add 2 / 5 of the required volume of deionized water or purified water into the preparation tank, heat to 40 degrees, add 70g / L nickel sulfate and stir to dissolve it;
[0024] b. In another small container, stir and dissolve 40 / L zinc sulfate with a small amount of purified water or deionized water at a temperature of 40 degrees, and stir it into the preparation tank after dissolution;
[0025] c. In another small container, stir and dissolve 25g / L boric acid with a small amount of pure water or deionized water at a temperature of 95 degrees, and stir and add it to the preparation tank after dissolving;
[0026] d. In another small container, stir and dissolve 40g / L ammonium nickel sulfate with a small amount of pure water or deionized water at a temperature of 40 degrees, and stir it into the preparation tank after dissolving; ...
Embodiment 2
[0035] A kind of preparation method that is applicable to above-mentioned electroplating liquid, prepares according to the following steps:
[0036] a. Add 1 / 2 of the required volume of deionized water or purified water to the preparation tank, heat to 45 degrees, add 85g / L nickel sulfate and stir to dissolve it;
[0037] b. In another small container, stir and dissolve 45g / L zinc sulfate with a small amount of pure water or deionized water at a temperature of 45 degrees, and stir it into the preparation tank after dissolution;
[0038] c. In another small container, stir and dissolve 30g / L boric acid with a small amount of pure water or deionized water at a temperature of 97 degrees, and stir it into the preparation tank after dissolving;
[0039] d. In another small container, stir and dissolve 50g / L ammonium nickel sulfate with a small amount of pure water or deionized water at a temperature of 45 degrees, and stir it into the preparation tank after dissolving;
[0040] e....
Embodiment 3
[0048] A kind of preparation method that is applicable to above-mentioned electroplating liquid, prepares according to the following steps:
[0049] a. Add 3 / 5 of the required volume of deionized water or purified water to the preparation tank, heat to 50 degrees, add 100g / L nickel sulfate and stir to dissolve it;
[0050] b. In another small container, stir and dissolve 50g / L zinc sulfate with a small amount of pure water or deionized water at a temperature of 50 degrees, and stir it into the preparation tank after dissolving;
[0051] c. In another small container, stir and dissolve 35g / L boric acid with a small amount of purified water or deionized water at a temperature of 99 degrees, and stir it into the preparation tank after dissolving;
[0052] d. In another small container, stir and dissolve 60g / L ammonium nickel sulfate with a small amount of pure water or deionized water at a temperature of 50 degrees, and stir it into the preparation tank after dissolving;
[0053...
PUM
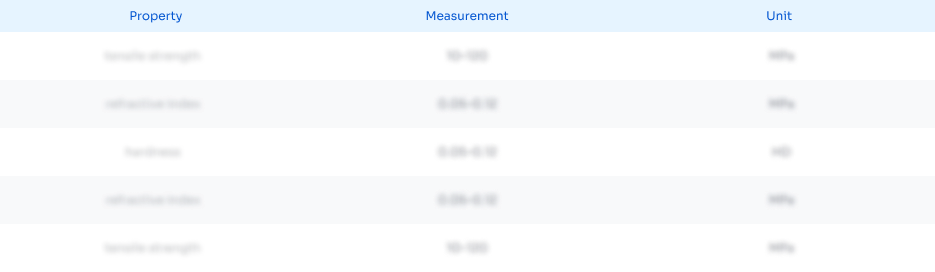
Abstract
Description
Claims
Application Information

- Generate Ideas
- Intellectual Property
- Life Sciences
- Materials
- Tech Scout
- Unparalleled Data Quality
- Higher Quality Content
- 60% Fewer Hallucinations
Browse by: Latest US Patents, China's latest patents, Technical Efficacy Thesaurus, Application Domain, Technology Topic, Popular Technical Reports.
© 2025 PatSnap. All rights reserved.Legal|Privacy policy|Modern Slavery Act Transparency Statement|Sitemap|About US| Contact US: help@patsnap.com