Polymer insulator material and preparation method thereof
A technology of insulators and polymers, applied in the direction of organic insulators, insulators, plastic/resin/wax insulators, etc., can solve the problems of electrical aging resistance, low partial discharge breakdown performance, poor nonlinear conductivity of composite materials, and no internal resistance. Charge performance and other issues to achieve the effect of increasing capture and detrapping time, improving interface compatibility, and weakening surface polarity
- Summary
- Abstract
- Description
- Claims
- Application Information
AI Technical Summary
Problems solved by technology
Method used
Image
Examples
Embodiment 1
[0031] Step 1: Pretreatment of thermoplastic polyimide molding powder: Weigh a preset amount of polyimide molding powder, and then place it in a vacuum drying oven for 24 hours at a drying temperature of 120°C and a vacuum degree of 10Pa to obtain The raw material of polyimide matrix after pretreatment;
[0032] Step 2: Cold press forming: put the pure polyimide material powder dried in step 1 into a mold for cold press forming, the forming pressure is 10MPa, and the duration is 15s;
[0033] Step 3: Segmented high temperature and high pressure molding: put the sample after cold pressing in step 2 into a molding machine for segmental high temperature and high pressure molding, starting from room temperature for 60 minutes to 270°C, and maintaining high pressure at 10MPa; 270°C, 10MPa Keep it warm for 20 minutes, at this time, the pure polyimide material is in a molten state; then take 5 minutes to raise the temperature to 300°C, hold it for 40 minutes, and keep the high pressu...
Embodiment 2
[0035] Step 1: Nano-zinc oxide filler dispersion and surface treatment: first mix ethanol and deionized water in a ratio of 95:5, add a coupling agent to prepare an alcoholic aqueous solution containing a coupling agent, and then add nano-zinc oxide powder to the In mixed alcohol aqueous solution containing coupling agent. Wherein the amount of the coupling agent is 3% of the mass of the nanometer zinc oxide powder. Then the above mixed solution was placed in an ultrasonic oscillator for ultrasonic oscillation and combined with high-speed stirring to disperse the inorganic particles for 30 minutes, such as figure 1 shown. Then put the above-dispersed suspension into a vacuum drying oven for drying treatment, the drying temperature is 105 ° C, the vacuum degree is 10 Pa, and the modified inorganic nano-zinc oxide powder is obtained by grinding. The coupling agent is γ-aminopropyl Triethoxysilane.
[0036] Thermoplastic polyimide molding powder pretreatment, weigh the polyimi...
Embodiment 3
[0041] Step 1: Nano-zinc oxide filler dispersion and surface treatment: first mix ethanol and deionized water in a ratio of 95:5, add a coupling agent to prepare an alcoholic aqueous solution containing a coupling agent, and then add nano-zinc oxide powder to the In mixed alcohol aqueous solution containing coupling agent. Wherein the amount of the coupling agent is 3% of the mass of the nanometer zinc oxide powder. Then the above mixed solution was placed in an ultrasonic oscillator for ultrasonic oscillation and combined with high-speed stirring to disperse the inorganic particles for 30 minutes, such as figure 1 shown. Then put the above-dispersed suspension into a vacuum drying oven for drying treatment, the drying temperature is 105 ° C, the vacuum degree is 10 Pa, and the modified inorganic nano-zinc oxide powder is obtained by grinding. The coupling agent is γ-aminopropyl Triethoxysilane.
[0042] Thermoplastic polyimide molding powder pretreatment, weigh the polyimi...
PUM
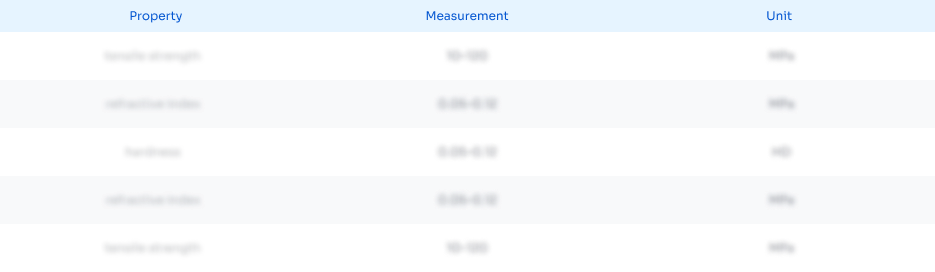
Abstract
Description
Claims
Application Information

- Generate Ideas
- Intellectual Property
- Life Sciences
- Materials
- Tech Scout
- Unparalleled Data Quality
- Higher Quality Content
- 60% Fewer Hallucinations
Browse by: Latest US Patents, China's latest patents, Technical Efficacy Thesaurus, Application Domain, Technology Topic, Popular Technical Reports.
© 2025 PatSnap. All rights reserved.Legal|Privacy policy|Modern Slavery Act Transparency Statement|Sitemap|About US| Contact US: help@patsnap.com