Mending material of glass furnace
A glass kiln and repair material technology, applied in the field of refractory materials, can solve the problems of unsustainable repair time and low erosion resistance, and achieve the effects of low thermal conductivity, good heat resistance and erosion resistance, and not easy to peel off.
- Summary
- Abstract
- Description
- Claims
- Application Information
AI Technical Summary
Problems solved by technology
Method used
Examples
Embodiment 1
[0008] Glass kiln repair material, prepared from the following raw materials according to the ratio of parts by mass, 12 parts of zircon with a particle size of 0.5mm-0.25mm, 40 parts of zircon with a particle size of 0.25mm-0.15mm, and a particle size of 0.15mm-0.07mm 12 parts of zircon, 5 parts of zircon with a particle size of 0.07mm-0.05mm, 10 parts of silicon carbide, 5 parts of silica sol, 13 parts of aluminum dihydrogen phosphate, 1 part of low calcium aluminate cement, after mixing and ball milling Finally, glass kiln repair materials are obtained.
Embodiment 2
[0010] Glass kiln repair material, prepared from the following raw materials according to the ratio of parts by mass, 23 parts of zircon with a particle size of 0.5mm-0.25mm, 21 parts of zircon with a particle size of 0.25mm-0.15mm, and a particle size of 0.15mm-0.07mm 22 parts of zircon, 10 parts of zircon with a particle size of 0.07mm-0.05mm, 13 parts of silicon carbide, 10 parts of silica sol, 11 parts of aluminum dihydrogen phosphate, 0.7 parts of low calcium aluminate cement, after mixing and ball milling Finally, glass kiln repair materials are obtained.
Embodiment 3
[0012] Glass kiln repair material, prepared from the following raw materials according to the ratio of parts by mass, 20 parts of zircon with a particle size of 0.5mm-0.25mm, 30 parts of zircon with a particle size of 0.25mm-0.15mm, and a particle size of 0.15mm-0.07mm 18 parts of zircon, 8 parts of zircon with a particle size of 0.07mm-0.05mm, 15 parts of silicon carbide, 16 parts of silica sol, 9 parts of aluminum dihydrogen phosphate, 0.9 parts of low calcium aluminate cement, after mixing and ball milling Finally, glass kiln repair materials are obtained.
PUM
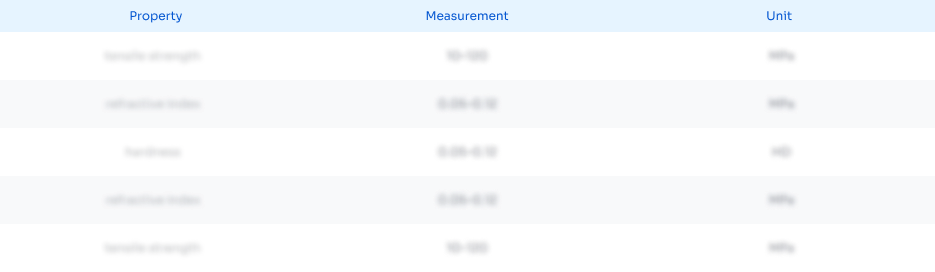
Abstract
Description
Claims
Application Information

- R&D
- Intellectual Property
- Life Sciences
- Materials
- Tech Scout
- Unparalleled Data Quality
- Higher Quality Content
- 60% Fewer Hallucinations
Browse by: Latest US Patents, China's latest patents, Technical Efficacy Thesaurus, Application Domain, Technology Topic, Popular Technical Reports.
© 2025 PatSnap. All rights reserved.Legal|Privacy policy|Modern Slavery Act Transparency Statement|Sitemap|About US| Contact US: help@patsnap.com