Unloading system of two-way feeding ore bin
A technology of ore silo and material feeding, which is applied in the field of two-way feeding ore silo unloading system, can solve the problems of increased project investment and operating cost, large impact of raw materials on the chute, and crowded plane layout on the silo, so as to reduce project investment and Production and operation costs, compact layout, and convenient crossing
- Summary
- Abstract
- Description
- Claims
- Application Information
AI Technical Summary
Problems solved by technology
Method used
Image
Examples
Embodiment 1
[0035] Such as Figure 1-5 As shown, the two-way feeding ore bunker unloading system of this embodiment includes two rows of ore bins 12, two corridors 13, 14 arranged at both ends of the two rows of ore bins, and two corridors 13, 14 respectively connected Belt conveyors 8, 9 and two bi-directional distributing and unloading vehicles 20, 30 matched with the two belt conveyors; the two belt conveyors 8, 9 are arranged in parallel, and the two belt conveyors 8, 9 run in opposite directions ;
[0036] Two-way distributing and unloading vehicles 20, 30 include vehicle frames 3, 3a, distributing devices and unloading devices arranged on the vehicle frames and reversible belt conveyors 4, 4a; Traveling mechanism 1, 11, 1a, 11a; the frame includes two sub-frames facing oppositely, and the tails of the two sub-frames are connected to each other; the material distribution device includes material distribution funnels 51, 5a, idler roller groups 6a, 61 and redirection Drum sets 7a, 7...
Embodiment 2
[0055] On the basis of the above-mentioned embodiment, the reversing roller group 6, 61, 6a, 61a includes the first roller arranged in the discharge funnel or the distribution funnel and the second roller arranged in front of the first roller; It includes several idlers arranged in sequence from front to back and from low to high.
[0056] The second roller is arranged on the front and lower side of the first roller, so that the belt conveyor belt between the first roller and the second roller can be at a certain angle to the vertical direction, so that the materials can be easily unloaded into the distribution funnel 5a, 51 or unloaded. Material funnel 5,51a, supporting roller group 7,71,7a, 71a are arranged from front to back, from low to high, so that the belts of belt conveyors 8,9 can be raised upwards at first before unloading, which is the second improvement. Provide adequate position to the pulley for belt redirection and unloading.
Embodiment 3
[0058] On the basis of the above embodiments, each idler roller and the first roller of the idler roller group 7, 71, 7a, 71a have a common cut surface, and the common cut surface is above each idler roller and the first roller.
[0059] Each idler and the first roller have a common cut surface on the upper side, so that the belt of the belt conveyor is arranged along the common cut surface, which can reduce the direction change of the belt conveyor 8, 9, and the reduction of the direction change can reduce resistance and save energy. energy.
PUM
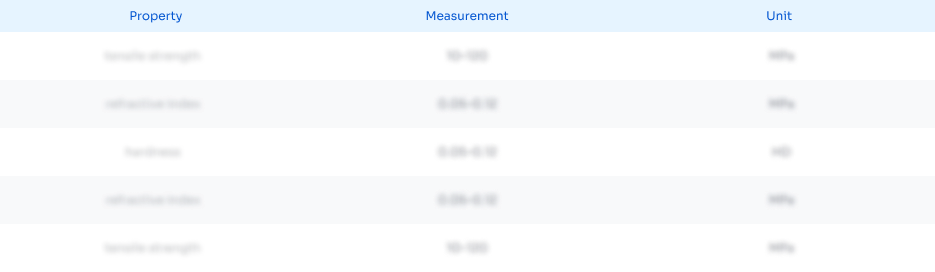
Abstract
Description
Claims
Application Information

- Generate Ideas
- Intellectual Property
- Life Sciences
- Materials
- Tech Scout
- Unparalleled Data Quality
- Higher Quality Content
- 60% Fewer Hallucinations
Browse by: Latest US Patents, China's latest patents, Technical Efficacy Thesaurus, Application Domain, Technology Topic, Popular Technical Reports.
© 2025 PatSnap. All rights reserved.Legal|Privacy policy|Modern Slavery Act Transparency Statement|Sitemap|About US| Contact US: help@patsnap.com