Breathable and warm air layer fabric
An air layer and fabric technology, applied in the field of fabrics, can solve the problems of loose fiber structure, which is not conducive to the shape retention of hollow fabrics, and achieve the effect of stable hole pattern, improved air permeability and moisture drainage performance, and not easy to fluff
- Summary
- Abstract
- Description
- Claims
- Application Information
AI Technical Summary
Problems solved by technology
Method used
Image
Examples
Embodiment 1
[0024] The air-permeable and warm-keeping air layer fabric of embodiment 1 is bonded or sewed by the hollow fabric and the air layer auxiliary material, and the preparation method of the hollow fabric comprises the following steps:
[0025] S1: Immerse the dry wool fabric in the ionic liquid containing soluble rare earth chloride lanthanum chloride, heat in microwave for 2 minutes, cool down to room temperature, keep it for 20 minutes, take out the wool fabric, wash it with ethanol, and dry it; the ionic liquid and chloride The weight ratio of rare earth is 1:0.0005.
[0026] S2: Configure the chitosan zinc sol finishing solution. The main components of the chitosan zinc sol finishing solution are chitosan, zinc dioxide, organic polyacids, and water. The pH of the chitosan zinc sol finishing solution is 3.5. The percentage by weight of chitosan in the polysaccharide zinc sol finishing solution is 0.5%, and the zinc content of the chitosan zinc sol finishing solution is 1.5%; ...
Embodiment 2
[0031] The difference between embodiment 2 and embodiment 1 is:
[0032] S1: Microwave heating for 5 minutes, keep for 40 minutes; soluble rare earth chloride is a mixture of neodymium chloride and gadolinium chloride 1:1. The weight ratio of the ionic liquid to the rare earth chloride is 1:0.001; the soluble rare earth chloride is a mixture of praseodymium chloride and samarium chloride, and the praseodymium chloride accounts for 20% by weight of the soluble rare earth chloride.
[0033] S2: The pH of the chitosan zinc sol finishing solution is 5, the weight percentage of chitosan in the chitosan zinc sol finishing solution is 3%, and the zinc content of the chitosan zinc sol finishing solution is 3.5%;
[0034] S3: Heating to 70°C, under heat preservation, the rolling liquid to the remaining rate is 85%, and the number of padding is 2 times;
[0035] S4: Baking and drying the fabric obtained in S3 at 120°C.
[0036] In the preparation process of the chitosan zinc sol finishi...
Embodiment 3
[0039] The difference between embodiment 3 and embodiment 2 is:
[0040] S1: Microwave heating for 3 minutes and keeping for 30 minutes; soluble rare earth chloride is a mixture of neodymium chloride and gadolinium chloride 1:1; the weight ratio of ionic liquid to rare earth chloride is 1:0.005; soluble rare earth chloride is praseodymium chloride and Samarium chloride is mixed, and praseodymium chloride accounts for 50% by weight of soluble rare earth chloride.
[0041] S2: The pH of the chitosan zinc sol finishing solution is 4.2, the weight percentage of chitosan in the chitosan zinc sol finishing solution is 1.7%, and the zinc content of the chitosan zinc sol finishing solution is 2.5%;
[0042] S3: Heating to 65°C, rolling liquid to the remaining rate of 80% under heat preservation, and the number of padding is 2 times;
[0043] S4: Baking and drying the fabric obtained in S3 at 110°C.
[0044] In the preparation process of the chitosan zinc sol finishing solution in S2...
PUM
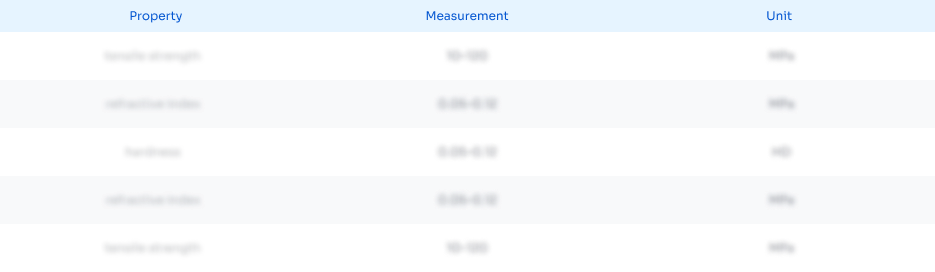
Abstract
Description
Claims
Application Information

- R&D
- Intellectual Property
- Life Sciences
- Materials
- Tech Scout
- Unparalleled Data Quality
- Higher Quality Content
- 60% Fewer Hallucinations
Browse by: Latest US Patents, China's latest patents, Technical Efficacy Thesaurus, Application Domain, Technology Topic, Popular Technical Reports.
© 2025 PatSnap. All rights reserved.Legal|Privacy policy|Modern Slavery Act Transparency Statement|Sitemap|About US| Contact US: help@patsnap.com