Methanol diesel fuel and preparation method thereof
A diesel and methanol technology, applied in the petroleum industry, liquid carbon-containing fuels, fuel additives, etc., can solve the problem of diesel engine exhaust odor, etc., and achieve the effects of improved PM emissions, long storage period, and good combustion performance
- Summary
- Abstract
- Description
- Claims
- Application Information
AI Technical Summary
Problems solved by technology
Method used
Image
Examples
Embodiment 1
[0016] Example 1: a, successively take 27 kg of diethyl alcohol formal, 7 kg of dimethylacetamide, 11 kg of secondary alcohol polyoxyethylene ether (S-50), 14 kg of caprylic acid glyceride, tetradecyl tris Add 13 kg of methyl ammonium bromide to Hefei Shengyuan SYFS4.0-22 high-speed disperser at 30-35°C, and stir for 3-5 minutes;
[0017] b. Take 40 kg of propylene glycol methyl ether, 3.4 kg of sec-butyl acetate, 13 kg of cocoamine polyoxyethylene ether (AC-1203), 16 kg of propynyl alcohol, and 4.5 kg of nano-magnesium hydroxide with an average particle size of 20nm. Add Hefei Shengyuan SYFS4.0-22 high-speed disperser at 30-35°C and stir for 2-3 minutes; ~80 minutes;
[0018] c. Add 150 kg of methanol and the mixture in step b to Hefei Shengyuan SYFS4.0-22 high-speed disperser and stir for 3 to 5 minutes; then add the mixture in step a and 700 kg of No. 0 diesel oil, using Hangzhou Chenggong Ultrasonic Equipment Co., Ltd. YPS57 ultrasonic stirrer, under the condition of 55 ...
Embodiment 2
[0019] Example 2: a, successively take 25 kilograms of diethyl alcohol formal, 6 kilograms of dimethylacetamide, 10 kilograms of secondary alcohol polyoxyethylene ether (S-50), 13 kilograms of caprylic acid glyceride, tetradecyl three Add 12 kg of methyl ammonium bromide to a SYFS4.0-22 high-speed disperser at 30-35°C, and stir for 3-5 minutes;
[0020] b. Take 30 kg of propylene glycol methyl ether, 3 kg of sec-butyl acetate, 12 kg of cocoamine polyoxyethylene ether (AC-1203), 15 kg of propynyl alcohol, and 4 kg of nano-magnesium hydroxide with an average particle size of 20nm. Add SYFS4.0-22 high-speed disperser at 30-35°C and stir for 2-3 minutes; then use YPS57 ultrasonic agitator to stir for 60-80 minutes at 62-65°C;
[0021] c. Add 140 kg of methanol and the mixture in step b to a SYFS4.0-22 high-speed disperser, and stir for 3 to 5 minutes; then add the mixture in step a and 680 kg of No. 0 diesel oil, and use a YPS57 ultrasonic stirrer, Stir at 55-60°C for 100-120 min...
Embodiment 3
[0022] Example 3: a, successively take 30 kg of diethyl alcohol formal, 8 kg of dimethylacetamide, 12 kg of secondary alcohol polyoxyethylene ether (S-50), 15 kg of caprylic acid glyceride, tetradecyl tri Add 15 kg of methyl ammonium bromide to a SYFS4.0-22 high-speed disperser at 30-35°C, and stir for 3-5 minutes;
[0023] b. Take 50 kg of propylene glycol methyl ether, 4 kg of sec-butyl acetate, 15 kg of cocoamine polyoxyethylene ether (AC-1203), 18 kg of propynyl alcohol, and 5 kg of nano-magnesium hydroxide with an average particle size of 20nm. Add SYFS4.0-22 high-speed disperser at 30-35°C and stir for 2-3 minutes; then use YPS57 ultrasonic agitator to stir for 60-80 minutes at 62-65°C;
[0024] c. Add 160 kg of methanol and the mixture in step b to a SYFS4.0-22 high-speed disperser, and stir for 3 to 5 minutes; then add the mixture in step a and 730 kg of No. 0 diesel oil, and use a YPS57 ultrasonic stirrer, Stir at 55-60°C for 100-120 minutes, then cool and serve.
PUM
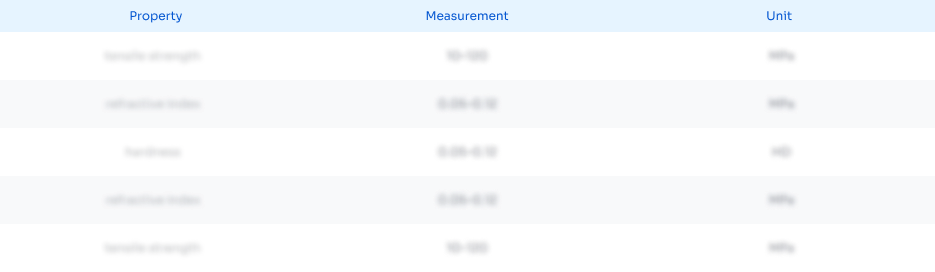
Abstract
Description
Claims
Application Information

- R&D
- Intellectual Property
- Life Sciences
- Materials
- Tech Scout
- Unparalleled Data Quality
- Higher Quality Content
- 60% Fewer Hallucinations
Browse by: Latest US Patents, China's latest patents, Technical Efficacy Thesaurus, Application Domain, Technology Topic, Popular Technical Reports.
© 2025 PatSnap. All rights reserved.Legal|Privacy policy|Modern Slavery Act Transparency Statement|Sitemap|About US| Contact US: help@patsnap.com