Special-shaped lens machining method based on computer aided manufacturing (CAM)
A special-shaped lens and processing method technology, applied in metal processing equipment, manufacturing tools, grinding machines, etc., can solve the problems of difficult processing of special-shaped lenses, low efficiency, low precision, etc., achieve good application prospects, convenient operation, and reduce processing waste rate effect
- Summary
- Abstract
- Description
- Claims
- Application Information
AI Technical Summary
Problems solved by technology
Method used
Image
Examples
Embodiment 1
[0035] The shape of the special-shaped lens to be processed in this embodiment is as follows: figure 1 , 2 As shown, the process requirements are (length unit is mm):
[0036] size: 27.2±0.1, 27.2±0.1;
[0037] Arc radius: R52.645±0.1, R38.355±0.1;
[0038] Round: R1;
[0039] Angle: 160°±2', 160°±2';
[0040] Roughness: Ra3.2.
[0041] The CAM-based special-shaped lens processing method of the present embodiment comprises the following steps:
[0042] 1) UG7.5 establishes a rotationally symmetrical mirror blank model (circle) of φ50.6mm, one side is a plane (the plane is the mounting surface for fitting with the tooling), the other side is a convex surface, and the radius of the curved surface is 66.385mm; in accordance with figure 1 , 2 And process requirements, cut into the target special-shaped lens model;
[0043] 2) Use the right-handed coordinate system, such as image 3 As shown, find the rotation axis of the circular mirror blank model before cutting, and ...
PUM
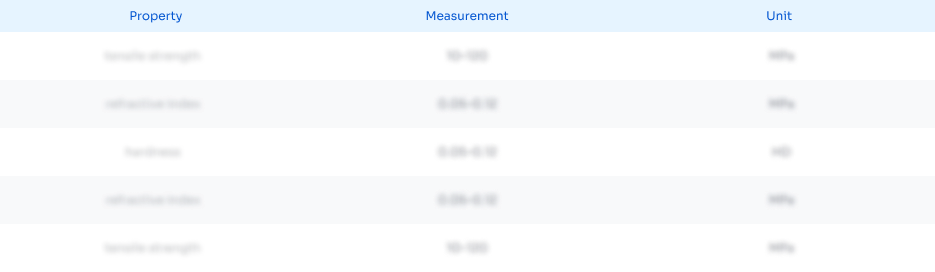
Abstract
Description
Claims
Application Information

- Generate Ideas
- Intellectual Property
- Life Sciences
- Materials
- Tech Scout
- Unparalleled Data Quality
- Higher Quality Content
- 60% Fewer Hallucinations
Browse by: Latest US Patents, China's latest patents, Technical Efficacy Thesaurus, Application Domain, Technology Topic, Popular Technical Reports.
© 2025 PatSnap. All rights reserved.Legal|Privacy policy|Modern Slavery Act Transparency Statement|Sitemap|About US| Contact US: help@patsnap.com