Low-temperature vacuum diffusion connecting method for copper and zinc-based alloy
A technology of vacuum diffusion and connection method, which is applied in the direction of welding equipment, metal processing equipment, welding/welding/cutting items, etc. It can solve the problems of poor plasticity of joints, great difficulty in good bonding, and easy generation of air holes, etc., to achieve interface Combining Stability, Reliable Performance, and High Productivity
- Summary
- Abstract
- Description
- Claims
- Application Information
AI Technical Summary
Problems solved by technology
Method used
Examples
Embodiment 1
[0031] The T2 red copper with a thickness of 2mm and the ZA-8 zinc-based alloy with a thickness of 2mm are subjected to low-temperature vacuum diffusion connection, and the workpiece size is 40mm×80mm.
[0032] The specific process steps are as follows:
[0033] (1) Surface cleaning before welding
[0034] Use No. 150 and No. 280 metallographic sandpaper to polish the surface to be welded of the T2 copper plate and the ZA-8 zinc-based alloy plate to ensure that the test plate is smooth and clean. Use acetone to clean the surface of the test plate to remove oil and scale. Use 15% HCl to pickle the copper plate for 4 minutes, then rinse with alcohol, and dry it with a hair dryer before use to ensure that the surface of the test plate is clean and dry.
[0035] (2) Vacuum diffusion connection
[0036] Place the cleaned copper plate and the zinc-based alloy plate overlappingly between the upper and lower pressure heads of the diffusion connection, put them into the vacuum furnac...
Embodiment 2
[0040] The T2 red copper with a thickness of 4mm and the ZA-12 zinc-based alloy with a thickness of 3mm are connected by low-temperature vacuum diffusion welding, and the workpiece size is 60mm×60mm.
[0041] The specific process steps are as follows:
[0042] (1) Surface cleaning before welding
[0043] Use No. 100 and No. 250 metallographic sandpaper to polish the surface of the T2 copper plate and ZA-12 zinc-based alloy plate to be welded to ensure that the test plate is smooth and clean. Use acetone to clean the surface of the test plate to remove oil and scale. Use 5% HCl to pickle the copper plate for 6 minutes, then rinse with alcohol, and dry it with a hair dryer before use to ensure that the surface of the test plate is clean and dry.
[0044] (2) Vacuum diffusion connection
[0045] Place the cleaned copper plate and the zinc-based alloy plate overlappingly between the upper and lower pressure heads of the diffusion connection, put them into the vacuum furnace of t...
Embodiment 3
[0049] The T2 red copper with a thickness of 2mm and the ZA-8 zinc-based alloy with a thickness of 2mm are vacuum diffusion connected, and the workpiece size is 40mm×80mm.
[0050] The specific process steps are as follows:
[0051] (1) Surface cleaning before welding
[0052] Use No. 150 and No. 280 metallographic sandpaper to polish the surface to be welded of the T2 copper plate and the ZA-8 zinc-based alloy plate to ensure that the test plate is smooth and clean. Use acetone to clean the surface of the test plate to remove oil and scale. Use 15% HCl to pickle the copper plate for 4 minutes, then rinse with alcohol, and dry it with a hair dryer before use to ensure that the surface of the test plate is clean and dry.
[0053] (2) Vacuum diffusion connection
[0054] Place the cleaned copper plate and the zinc-based alloy plate overlappingly between the upper and lower pressure heads of the diffusion connection, put them into the vacuum furnace of the vacuum diffusion connec...
PUM
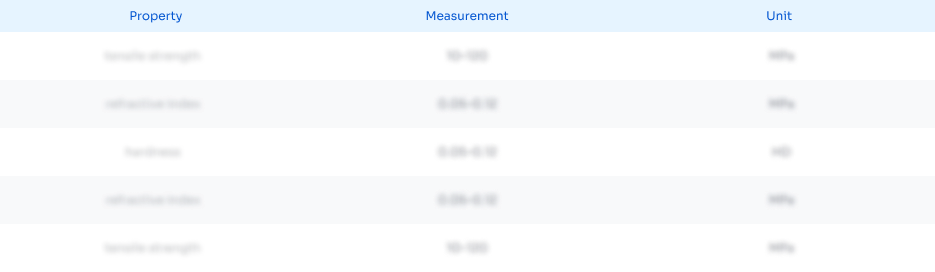
Abstract
Description
Claims
Application Information

- R&D Engineer
- R&D Manager
- IP Professional
- Industry Leading Data Capabilities
- Powerful AI technology
- Patent DNA Extraction
Browse by: Latest US Patents, China's latest patents, Technical Efficacy Thesaurus, Application Domain, Technology Topic, Popular Technical Reports.
© 2024 PatSnap. All rights reserved.Legal|Privacy policy|Modern Slavery Act Transparency Statement|Sitemap|About US| Contact US: help@patsnap.com