Non-contact induction power supply device used for ultrasonic milling processing
A technology of milling processing and induction power supply, which is applied to circuit devices, electrical components, etc., can solve the problems of low rotation stability of rotating parts, limited rotation speed, and inability to ensure stable and high reliability ultrasonic milling operations.
- Summary
- Abstract
- Description
- Claims
- Application Information
AI Technical Summary
Problems solved by technology
Method used
Image
Examples
Embodiment 1
[0120] attached Figure 9 It is a specific embodiment of a non-contact inductive power supply device for ultrasonic milling of the present invention.
[0121] According to attached Figure 9 It can be seen that the non-contact inductive power supply device consists of two parts, the primary side 3 and the secondary side 4 .
[0122] The primary side 3 is fixedly mounted on the spindle base 7 of the CNC machining center and connected to the ultrasonic power supply 1; the secondary side 4 is fixedly mounted on the standard spindle ultrasonic milling tool handle 9 and integrated with the standard spindle ultrasonic milling cutter The ultrasonic vibration system 6 inside the handle 9 is connected.
[0123] As shown in accompanying drawing 2 (a), the spatial positional relation of described primary side 3 and described secondary side 4 is arranged as inner and outer concentric circles, and described primary side 3 is outside described secondary side 4; There is no mechanical con...
PUM
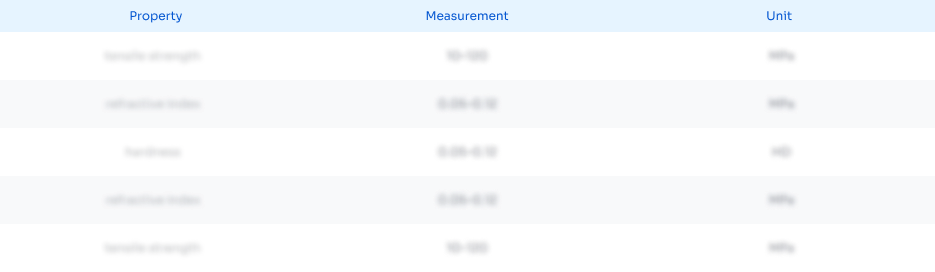
Abstract
Description
Claims
Application Information

- R&D Engineer
- R&D Manager
- IP Professional
- Industry Leading Data Capabilities
- Powerful AI technology
- Patent DNA Extraction
Browse by: Latest US Patents, China's latest patents, Technical Efficacy Thesaurus, Application Domain, Technology Topic, Popular Technical Reports.
© 2024 PatSnap. All rights reserved.Legal|Privacy policy|Modern Slavery Act Transparency Statement|Sitemap|About US| Contact US: help@patsnap.com