Method for preparing unsaturated polyester composite material filled with modified calcium carbonate
A polyester composite material, unsaturated technology, used in the field of composite materials, can solve the problems of poor impact resistance and aging resistance, product performance degradation, etc., to achieve improved heat resistance and aging resistance, and enhanced aging resistance. Effects of strength and toughness
- Summary
- Abstract
- Description
- Claims
- Application Information
AI Technical Summary
Problems solved by technology
Method used
Examples
example 1
[0021] First, take 50g of calcium oxide and add it to a 1000mL beaker, then add 200mL of boiling water at 100°C to the beaker, mix and stir evenly to form Ca(OH) 2 After standing for 10 hours, filter the slurry with a 160-mesh sieve to remove impurities and large particles, and then transfer it to a 500mL three-necked sesame cake; respectively take 60g of polyethylene glycol and 6g of polyphosphoric acid and place them in a 500mL three-necked flask, and use a magnetic stirrer to Stir at room temperature for 30 minutes, and then put it in a water bath at 85°C to stir for 2 hours. After the reaction, cool the product in the bottle to room temperature, then take 10 g of the reacted product and add it to the above-mentioned flask, and stir it mechanically for 25 minutes. Afterwards, a mixed gas of carbon dioxide and nitrogen was passed into the bottle, and the reaction was carried out at room temperature. After the reaction was completed for 20 minutes, it was filtered, and the obt...
example 2
[0024] First, take 55g of calcium oxide and add it to a 1000mL beaker, then add 230mL of boiling water at 100°C to the beaker, mix and stir evenly to form Ca(OH) 2 After standing for 11 hours, filter the slurry with a 170-mesh sieve to remove impurities and large particles, and then transfer it into a 500mL three-necked sesame cake; respectively take 63g of polyethylene glycol and 6.5g of polyphosphoric acid and place them in a 500mL three-necked flask, and stir them with a magnetic force The device was stirred at room temperature for 35 minutes, and then placed in a water bath at 87°C to stir for 2.5 hours. After the reaction, the product in the bottle was cooled to room temperature, and then 13 g of the reacted product was added to the above-mentioned flask, and mechanically stirred. After 30 minutes, the mixed gas of carbon dioxide and nitrogen was passed into the bottle, and the reaction was carried out at room temperature. After the reaction was completed for 25 minutes, i...
example 3
[0027] First, take 60g of calcium oxide and add it to a 1000mL beaker, then add 240mL of boiling water at 100°C to the beaker, mix and stir evenly to form Ca(OH) 2 After standing for 12 hours, filter the slurry with a 180-mesh sieve to remove impurities and large particles, and then transfer it into a 500mL three-necked sesame cake; respectively take 65g of polyethylene glycol and 7g of polyphosphoric acid in a 500mL three-necked flask, and use a magnetic stirrer to Stir at room temperature for 40 minutes, then put it in a water bath at 90°C and stir for 3 hours. After the reaction, cool the product in the bottle to room temperature, then add 15 g of the reacted product to the above-mentioned flask, and stir mechanically for 35 minutes. After that, a mixed gas of carbon dioxide and nitrogen was passed into the bottle, and the reaction was carried out at room temperature. After the reaction was completed for 30 minutes, it was filtered, and the obtained filter residue was washed...
PUM
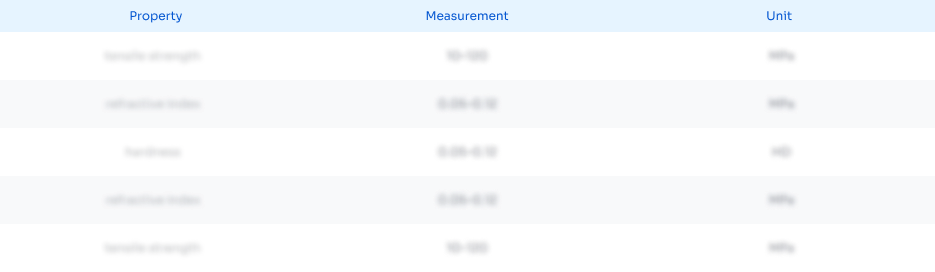
Abstract
Description
Claims
Application Information

- R&D Engineer
- R&D Manager
- IP Professional
- Industry Leading Data Capabilities
- Powerful AI technology
- Patent DNA Extraction
Browse by: Latest US Patents, China's latest patents, Technical Efficacy Thesaurus, Application Domain, Technology Topic, Popular Technical Reports.
© 2024 PatSnap. All rights reserved.Legal|Privacy policy|Modern Slavery Act Transparency Statement|Sitemap|About US| Contact US: help@patsnap.com