A method for recycling waste lubricating oil
A technology of waste lubricating oil and lubricating oil, which is applied in the direction of hydrocarbon oil treatment products, hydrocarbon oil treatment, lubricating composition, etc., can solve the problems of low utilization rate of waste lubricating oil raw materials, poor product properties, etc., and achieve the value of large-scale industrial promotion, The effect of good product properties and moderate conditions
- Summary
- Abstract
- Description
- Claims
- Application Information
AI Technical Summary
Problems solved by technology
Method used
Image
Examples
Embodiment 1
[0039] A method for recycling waste lubricating oil, comprising the following steps:
[0040] (1) Solvent treatment: Stir and mix the waste lubricating oil and tetrahydrofuran methanol with a volume ratio of 1:1.5, stir for 1 hour, let stand for 8 hours to separate layers, centrifuge the upper lubricating oil, and remove the solvent by vacuum distillation of the oil sample. 90℃, pressure -0.1MPa;
[0041] (2) Membrane separation: The waste lubricating oil after solvent treatment first enters the first-stage membrane module, and the material pressure entering the first-stage membrane module is 2.0MPa, and the temperature is 65°C; then enters the second-stage membrane module, enters The pressure of the second-stage membrane module is 1.2MPa, and the temperature is 98°C; then it enters the next step of hydrogenation upgrading unit; the membrane element of the first-stage membrane module is a ceramic microfiltration membrane, and the membrane element of the second-stage membrane m...
Embodiment 2
[0048] A method for recycling waste lubricating oil, comprising the following steps:
[0049] (1) Solvent treatment: Stir and mix the waste lubricating oil and tetrahydrofuran methanol with a volume ratio of 1:1, stir for 0.5h, let stand for 8h to separate layers, centrifuge the upper layer of lubricating oil, and distill the oil sample under reduced pressure to remove the solvent, then distill under reduced pressure Temperature 90℃, pressure -0.1MPa;
[0050] (2) Membrane separation: The waste lubricating oil after solvent treatment first enters the first-stage membrane module, and the material pressure entering the first-stage membrane module is 1.5MPa, and the temperature is 70°C; then enters the second-stage membrane module, enters The pressure of the second-stage membrane module is 1MPa, and the temperature is 100°C; then it enters the next step of hydrogenation reforming unit; the membrane element of the first-stage membrane module is a ceramic microfiltration membrane, ...
Embodiment 3
[0057] A method for recycling waste lubricating oil, comprising the following steps:
[0058] (1) Solvent treatment: Stir and mix the waste lubricating oil and tetrahydrofuran methanol with a volume ratio of 1:2, stir for 1.5 hours, let stand for 8 hours to separate layers, centrifuge the upper layer of lubricating oil, and distill the oil sample under reduced pressure to remove the solvent, then distill under reduced pressure Temperature 90℃, pressure -0.1MPa;
[0059] (2) Membrane separation: The waste lubricating oil after solvent treatment first enters the first-stage membrane module, and the material pressure entering the first-stage membrane module is 2.5MPa, and the temperature is 60°C; then enters the second-stage membrane module, enters The pressure of the second-stage membrane module is 1.5MPa, and the temperature is 95°C; then it enters the next step of hydrogenation upgrading unit; the membrane element of the first-stage membrane module is a ceramic microfiltration...
PUM
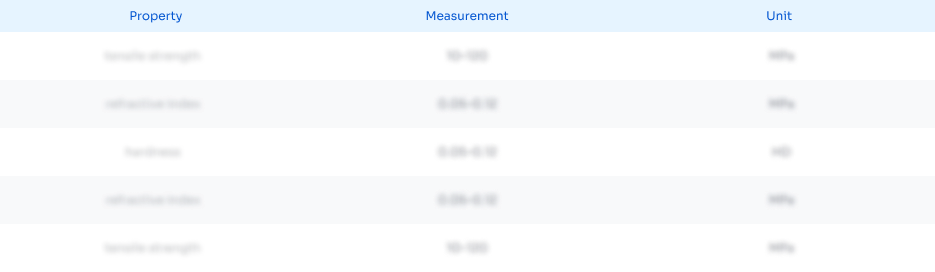
Abstract
Description
Claims
Application Information

- R&D
- Intellectual Property
- Life Sciences
- Materials
- Tech Scout
- Unparalleled Data Quality
- Higher Quality Content
- 60% Fewer Hallucinations
Browse by: Latest US Patents, China's latest patents, Technical Efficacy Thesaurus, Application Domain, Technology Topic, Popular Technical Reports.
© 2025 PatSnap. All rights reserved.Legal|Privacy policy|Modern Slavery Act Transparency Statement|Sitemap|About US| Contact US: help@patsnap.com