Construction method of gradient silica surface microfluidic system
A microfluidic system, silica technology, applied in chemical instruments and methods, laboratory containers, laboratory utensils, etc., can solve the problem of not being able to convert interface free energy into droplet mechanical energy, etc., to enhance the capillary driving force Effect
- Summary
- Abstract
- Description
- Claims
- Application Information
AI Technical Summary
Problems solved by technology
Method used
Image
Examples
preparation example Construction
[0041] SiO 2 The preparation of the nano film layer is obtained by the hydrolysis of ethyl orthosilicate and ammonia water or silicon tetrachloride, and is carried out by chemical vapor deposition. Specifically, place two containers (two kinds of reagents with the same volume) and the sample obtained in step 1 in an airtight desiccator that are respectively multiplied by tetraethyl orthosilicate and ammonia water, or replace the reagent with silicon tetrachloride. The relative humidity is 60% RH, and the ambient temperature is 30°C, put it in a blast drying oven for 12-24 hours, take it out, heat-treat at 400-600°C for 1-3 hours, remove the soot layer and other organic matter, and cool it naturally for later use.
[0042] 3), Modified SiO with hydrophobic material 2 Nano film layer, forming a hydrophobic layer;
[0043] Hydrophobic material is selected from alkyltrichlorosilane (Cl 3 Si(CH 2 ) n CH 3 , n=8~16) chemical reagents. Soak the sample in 3-10mmol alkyltrichlor...
Embodiment 1
[0047] Step 1, get common glass slide, slide glass is soaked in piranha solution (98%H 2 SO 4and 30%H 2 o 2 , mixed in a ratio of 3:1), placed on a heating plate at 200°C and heated for 1 hour, after taking it out, use acetone, ethanol, and deionized water to perform ultrasonic purification at room temperature for 10 minutes each, and then blow dry with nitrogen .
[0048] Step 2. Place the cleaned glass slide at an angle of 45° at 0.5 cm above the candle flame for 5 seconds to obtain a porous network-like soot structure with a gradient.
[0049] Step 3. Place the obtained sample together with two containers multiplied by 4mL tetraethyl orthosilicate and 4mL ammonia water in a closed desiccator in a blast drying oven with a relative humidity of 60% RH and an ambient temperature of 30°C Placed in the middle for 24 hours, the hydrolysis of tetraethyl orthosilicate and ammonia water will generate SiO 2 Coated on the outside of soot particles to form SiO with a thickness of 2...
Embodiment 2
[0055] Embodiment 2 and embodiment 1 only generate SiO in step 3 2 The method of shelling is different. In Example 2, the obtained soot layer substrate was airtightly placed in a petri dish together with 100 μL of silicon tetrachloride solution, and placed in a blast drying oven with a relative humidity of 60% RH and an ambient temperature of 30° C. for 12 hours.
[0056] Other preparation method is the same as embodiment 1, also can be in SiO 2 A superhydrophilic-hydrophobic microfluidic channel is formed on the surface of the membrane layer.
PUM
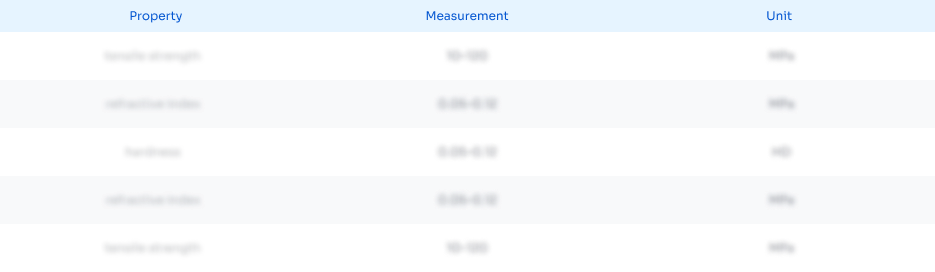
Abstract
Description
Claims
Application Information

- Generate Ideas
- Intellectual Property
- Life Sciences
- Materials
- Tech Scout
- Unparalleled Data Quality
- Higher Quality Content
- 60% Fewer Hallucinations
Browse by: Latest US Patents, China's latest patents, Technical Efficacy Thesaurus, Application Domain, Technology Topic, Popular Technical Reports.
© 2025 PatSnap. All rights reserved.Legal|Privacy policy|Modern Slavery Act Transparency Statement|Sitemap|About US| Contact US: help@patsnap.com