Method for recycling tin from tin alkali solution
A technology of tin alkali and solution, which is applied in the field of recovering tin from tin alkali solution, can solve the problems of bringing in impurities and low precipitation efficiency, and achieve the effect of low temperature, high purity and high value
- Summary
- Abstract
- Description
- Claims
- Application Information
AI Technical Summary
Problems solved by technology
Method used
Examples
Embodiment 1
[0024] Taking the tin-containing waste residue of a tin-plating factory as the treatment object, its composition (wt%) is tin Sn: 28.25%, iron Fe: 3.51%, leaching with alkali solution, leaching temperature 30℃, leaching time 2h, alkali concentration 180g / L , The leachate composition (g / L) is tin Sn: 24.53g / L.
[0025] Heat the tin alkali solution to 90°C, add 200 mesh metal zinc powder according to the molar ratio of zinc Zn: tin Sn=3:1, and add a certain amount of copper oxide CuO additive, the dosage of copper oxide CuO is metal zinc powder The dosage is 0.01%, the replacement time is 1h, after the reaction is completed, filter while it is hot, the obtained filtrate components are zinc Zn: 21.08g / L, tin Sn: 0.098g / L, the filtrate is directly electrolyzed to recover zinc powder, zinc powder The recovery rate reaches 93.23%, and the tin content in the obtained filter residue is 85.82%, which is sold or subsequently processed.
Embodiment 2
[0027] Taking the tin-containing waste slag of a tin-plating factory as the processing object, its composition (wt%) is tin Sn: 32.17%, iron Fe: 1.30%, leaching with alkali solution, leaching temperature 50℃, leaching time 2h, alkali concentration 200g / L , The leachate composition (g / L) is tin Sn: 26.88g / L.
[0028] Heat the tin alkali solution to 70°C, add 200 mesh metal zinc powder according to the molar ratio of zinc Zn: tin Sn=2:1, and add a certain amount of antimony trichloride SbCl3 additive, the additive dosage is metal zinc powder The dosage is 0.1%, the replacement time is 1.5h, after the reaction is completed, filter while it is hot, the obtained filtrate components are zinc Zn: 20.25g / L, tin Sn: 0.085g / L, the filtrate is directly electrolyzed to recover zinc powder, zinc powder The recovery rate reached 95.08%, and the tin content in the obtained filter residue was 87.47%, which was sold or subsequently processed.
Embodiment 3
[0030] Taking the tinplate anode slime of a factory as the treatment object, its composition (wt%) is tin Sn: 15.25%, iron Fe: 18.51%, leaching with alkali solution, leaching temperature 70°C, leaching time 3h, alkali concentration 150g / L, leaching solution Composition (g / L) is tin Sn: 12.25g / L.
[0031] Heat the tin alkali solution to 50°C, add 200 mesh metal zinc powder according to the molar ratio of zinc Zn:tin Sn=1.5:1, and add a certain amount of copper oxide CuO, the dosage of copper oxide CuO is metal zinc powder 0.05% of the added amount, the replacement time is 2 hours, after the reaction is completed, filter while it is hot, the obtained filtrate components are zinc Zn: 11.54g / L, tin Sn: 0.073g / L, and the filtrate is directly electrolyzed to recover zinc powder, recovery of zinc powder The rate reaches 90.41%, and the tin content in the obtained filter residue is 89.18%, which is sold or subsequently processed.
PUM
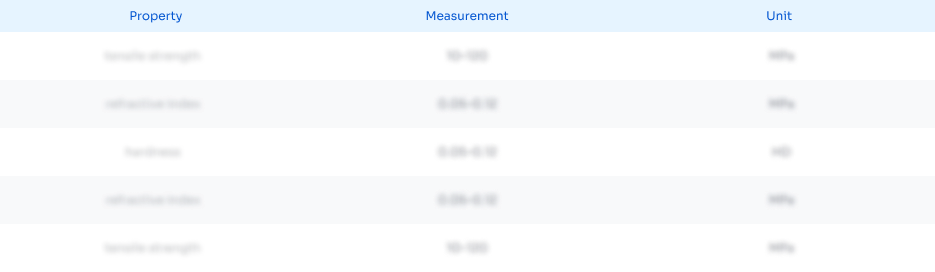
Abstract
Description
Claims
Application Information

- Generate Ideas
- Intellectual Property
- Life Sciences
- Materials
- Tech Scout
- Unparalleled Data Quality
- Higher Quality Content
- 60% Fewer Hallucinations
Browse by: Latest US Patents, China's latest patents, Technical Efficacy Thesaurus, Application Domain, Technology Topic, Popular Technical Reports.
© 2025 PatSnap. All rights reserved.Legal|Privacy policy|Modern Slavery Act Transparency Statement|Sitemap|About US| Contact US: help@patsnap.com