Attapulgite based 3D printer bracket and preparation method thereof
A 3D printer, attapulgite technology, applied in building components, building insulation materials, buildings, etc., can solve problems such as reducing the performance of 3D printers and prone to deformation
- Summary
- Abstract
- Description
- Claims
- Application Information
AI Technical Summary
Problems solved by technology
Method used
Examples
preparation example Construction
[0012] The invention provides a method for preparing an attapulgite soil-based 3D printer support, comprising:
[0013] 1) Calcining attapulgite, shells and black loam, then placing the calcined product in hydrochloric acid solution for acidification, filtering to take the filter cake, and then placing the filter cake under X-rays for activation treatment to obtain the activated product ;
[0014] 2) Epoxy resin, phenol furan resin, methyl cellulose, basic magnesium sulfate whisker, magnesium oxide, valine, glass fiber, pitch, sodium azulene sulfonate, potassium aluminum sulfate, thienopyrimidine, swelling Graphite, ozokerite, sodium humate and cocoic acid monoethanolamide were mixed, melted, and cooled to make an attapulgite-based 3D printer support.
[0015] In step 1) of the present invention, the specific conditions of calcination can be selected in a wide range, but in order to make the 3D printer support made have more excellent mechanical stability, preferably, in step...
Embodiment 1
[0026] 1) Mix attapulgite, shell and black loam in a weight ratio of 100:21:4.5 and calcinate at 515°C for 6.5h, then place the calcined product at 50°C in a hydrochloric acid solution with a concentration of 28% by weight (relative to In the described attapulgite of 100 parts by weight, the consumption of hydrochloric acid solution is 100 parts by weight), carry out acidification treatment 1.5h, filter and get filter cake, then filter cake is placed in X-ray (wavelength is 30 Angstroms) and temperature is Activation treatment was carried out for 50 minutes at 25°C to obtain the activated product;
[0027] 2) Bisphenol A type epoxy resin (weight average molecular weight is 7000), phenol furan resin (weight average molecular weight is 5000), activator, methyl cellulose, basic magnesium sulfate whisker, magnesium oxide, valine , glass fiber, asphalt, sodium azulene sulfonate, potassium aluminum sulfate, thienopyrimidine, expandable graphite, ozokerite, sodium humate and cocoic a...
Embodiment 2
[0029] 1) Mix attapulgite, shell and black loam in a weight ratio of 100:20:3.5 and calcinate at 500°C for 6h, then place the calcined product at 45°C in a hydrochloric acid solution with a concentration of 25% by weight (relative to 100 parts by weight of the attapulgite, the amount of hydrochloric acid solution is 80 parts by weight), acidified for 1h, filtered to get the filter cake, then the filter cake is placed in X-ray (wavelength is 20 Angstroms) and the temperature is 15 ° C Activation treatment was carried out for 45min under certain conditions to obtain an activated product;
[0030] 2) Bisphenol F type epoxy resin (weight average molecular weight is 6000), phenol furan resin (weight average molecular weight is 3000), activator, methyl cellulose, basic magnesium sulfate whisker, magnesium oxide, valine , glass fiber, asphalt, sodium azulene sulfonate, potassium aluminum sulfate, thienopyrimidine, expandable graphite, ozokerite, sodium humate and cocoic acid monoetha...
PUM
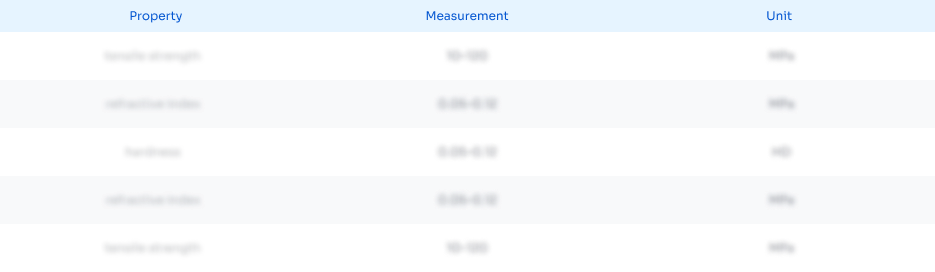
Abstract
Description
Claims
Application Information

- Generate Ideas
- Intellectual Property
- Life Sciences
- Materials
- Tech Scout
- Unparalleled Data Quality
- Higher Quality Content
- 60% Fewer Hallucinations
Browse by: Latest US Patents, China's latest patents, Technical Efficacy Thesaurus, Application Domain, Technology Topic, Popular Technical Reports.
© 2025 PatSnap. All rights reserved.Legal|Privacy policy|Modern Slavery Act Transparency Statement|Sitemap|About US| Contact US: help@patsnap.com