Novel carbonized wood production method
A production method and technology of carbonized wood, which are applied in the directions of wood treatment, wood impregnation, wood impregnation, etc., can solve the problems of poor waterproof performance, unsatisfactory termite resistance performance, etc., and achieve increased density, improved insect-proof and termite-proof performance, and improved mechanical strength. Effect
- Summary
- Abstract
- Description
- Claims
- Application Information
AI Technical Summary
Benefits of technology
Problems solved by technology
Method used
Examples
Embodiment 1
[0029] A novel carbonized wood production method, the steps are as follows:
[0030] 1. Selection: The modulus of sodium silicate is 1.4; the particle size range of nano-silica powder and nano-titanium dioxide powder is 10-80nm.
[0031] 2. Wood impregnation pretreatment
[0032] Put wood with a specification of 1200mm×130mm×30mm (length×width×thickness) in a vacuum treatment tank, first vacuumize the vacuum treatment tank for 0.6h; then inject sodium silicate solution: nano silica powder: nano Titanium dioxide powder: Zinc borate solution = 5:0.6:0.5:2 impregnation modification solution, after the tank to be treated is filled, apply a pressure of 1.5Mpa, and the pressure holding time is 2.4h; finally vacuum the tank for 1.4h Vacuumize, drain the impregnated modification liquid remaining on the wood, and take out the wood.
[0033] 3. Wood high temperature treatment
[0034] a) Preparatory stage: put the impregnated pretreated wood into the carbonization chamber of the carb...
Embodiment 2
[0042] A novel carbonized wood production method, the steps are as follows:
[0043] 1. Selection: The modulus of sodium silicate is 1.2; the particle size range of nano-silica powder and nano-titanium dioxide powder is 1-100nm.
[0044] 2. Wood impregnation pretreatment
[0045] Put wood with a specification of 1200mm×130mm×30mm (length×width×thickness) in a vacuum treatment tank, first vacuumize the vacuum treatment tank for 0.4h; then inject sodium silicate solution: nano silica powder: nano Titanium dioxide powder: Zinc borate solution = 4:0.5:0.3:1 immersion modification solution, after the tank to be treated is filled, apply a pressure of 1.2Mpa, and the pressure holding time is 2.1h; finally vacuum the tank for 1.1h Vacuumize, drain the impregnated modification liquid remaining on the wood, and take out the wood.
[0046] 3. Wood high temperature treatment
[0047] a) Preparatory stage: put the impregnated pretreated wood into the carbonization chamber of the carboni...
Embodiment 3
[0055] A novel carbonized wood production method, the steps are as follows:
[0056] 1. Selection: The modulus of sodium silicate is 1.6; the particle size range of nano-silica powder and nano-titanium dioxide powder is 20-70nm.
[0057] 2. Wood impregnation pretreatment
[0058] Put wood with a specification of 1200mm×130mm×30mm (length×width×thickness) in a vacuum treatment tank, first vacuumize the vacuum treatment tank for 0.8h; then inject sodium silicate solution: nano silica powder: nano Titanium dioxide powder: Zinc borate solution = 6:0.7:0.7:3 immersion modification solution, after the tank to be treated is filled, apply a pressure of 1.8Mpa, and the pressure holding time is 2.7h; finally vacuum the tank for 1.7h Vacuumize, drain the impregnated modification liquid remaining on the wood, and take out the wood.
[0059] 3. Wood high temperature treatment
[0060] a) Preparatory stage: put the impregnated pretreated wood into the carbonization chamber of the carboni...
PUM
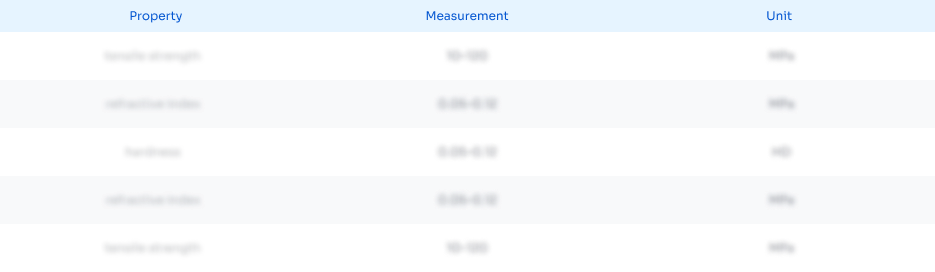
Abstract
Description
Claims
Application Information

- R&D Engineer
- R&D Manager
- IP Professional
- Industry Leading Data Capabilities
- Powerful AI technology
- Patent DNA Extraction
Browse by: Latest US Patents, China's latest patents, Technical Efficacy Thesaurus, Application Domain, Technology Topic, Popular Technical Reports.
© 2024 PatSnap. All rights reserved.Legal|Privacy policy|Modern Slavery Act Transparency Statement|Sitemap|About US| Contact US: help@patsnap.com