A kind of billet anti-oxidation coating and spraying method thereof
An anti-oxidation coating and casting slab technology, which is applied in the field of casting slab anti-oxidation coating and spraying of casting slab anti-oxidation coating at high temperature, can solve the problems of unstable use effect, poor anti-oxidation effect, and low economic benefit, and achieve Improve the effect of use, inhibit diffusion, and prevent corrosion
- Summary
- Abstract
- Description
- Claims
- Application Information
AI Technical Summary
Problems solved by technology
Method used
Examples
Embodiment 1
[0023] This example is a comparative example, which is a commonly used anti-oxidation coating and method.
[0024] The ratio of selected coatings is calculated by weight %: 30% Al 2 o 3 , 65% clay, 5% anhydrous water glass, add water to make a slurry for spraying. It is sprayed at room temperature, the steel type is welding wire steel, and the amount of slurry sprayed is 0.65kg / m 2 , the heating temperature is 1200°C, the holding time is 75 minutes, the yield of the slab is 98.05%, and the rest is oxidized burning and corrosion damage.
Embodiment 2
[0026] Use 30%Si 3 N 4 , 8% Fe, 30% Al 2 o 3 , 32% SiO 2 The composition of the anti-oxidation coating is processed and ground into a powder; the steel billet is also used to spray the paint on the billet at a temperature of 800°C by using a spray gun through the powder electrostatic spraying method, and the spraying amount is 0.65 kg / m 2 , and then heated in the furnace, the heating temperature is 1200 ° C, and the holding time is 75 minutes; the yield of the cast slab after rolling is 99.59%.
[0027] Through physical and chemical testing, the anti-oxidation coating of this embodiment melts and spreads at high temperature, forming a complete and dense double-layer protective film, and the cast slab produces very little iron oxide scale during the heating process, which is better than the conventional anti-oxidation coating and its spray coating. The yield of cast slab produced by the method is increased by 1.54%.
Embodiment 3
[0029] Choose 45% SiC, 10% Fe, 20% MgO, 25% SiO 2 The composition of the anti-oxidation coating is processed and ground into powder; the alloy steel billet is used, and the paint is sprayed on the billet at a temperature of 500 °C by using a spray gun through the powder electrostatic spraying method, and the spraying amount is 0.65kg / m 2 , and then heated in the furnace, the heating temperature is 1150 ° C, and the holding time is 75 minutes; the yield of the cast slab after rolling is 99.69%.
[0030] Through physical and chemical testing, the paint melted and spread at high temperature forms a complete and dense protective film, and the slab has less iron oxide scale, which increases the yield of the slab by 1.64%.
PUM
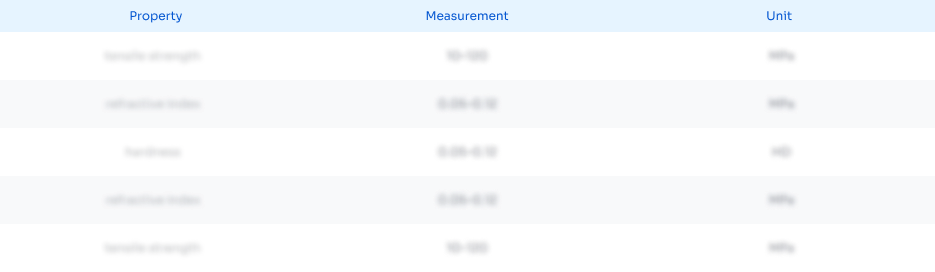
Abstract
Description
Claims
Application Information

- Generate Ideas
- Intellectual Property
- Life Sciences
- Materials
- Tech Scout
- Unparalleled Data Quality
- Higher Quality Content
- 60% Fewer Hallucinations
Browse by: Latest US Patents, China's latest patents, Technical Efficacy Thesaurus, Application Domain, Technology Topic, Popular Technical Reports.
© 2025 PatSnap. All rights reserved.Legal|Privacy policy|Modern Slavery Act Transparency Statement|Sitemap|About US| Contact US: help@patsnap.com