Zero-backlash low-noise transmission gear
A transmission gear, low-noise technology, applied in belts/chains/gears, components with teeth, portable lifting devices, etc., can solve pitting corrosion on tooth surfaces of enlarged gears, local plastic deformation of gluing, and difficult to eliminate gears Problems such as the backlash of the meshing parts of the gear teeth and the inability of the elastic gear to compensate radially can reduce the risk of failure, reduce the risk of broken teeth, and eliminate interference
- Summary
- Abstract
- Description
- Claims
- Application Information
AI Technical Summary
Problems solved by technology
Method used
Image
Examples
Embodiment 1
[0035] refer to figure 1 , this embodiment includes a driving wheel 1 and a driven wheel 2, the driving wheel 1 includes a driving wheel gear body 1-2 and a driving wheel gear tooth 1-1, and the driving wheel gear teeth 1-1 are evenly distributed on the driving wheel gear body 1 -2 on the peripheral edge; the driven wheel 2 includes a driven wheel gear body 2-2 and a driven wheel gear tooth 2-1, and the driven wheel gear tooth 2-1 is evenly distributed on the peripheral edge of the driven wheel gear body 2-2 The driven wheel gear tooth 2-1 meshes with the driving wheel gear tooth 1-1; the center of the driving wheel gear body 1-2 and the driven wheel gear body 2-2 are equipped with shaft holes; the driven wheel gear body 2-2 is close to The end face of the driven wheel gear tooth 2-1 root is provided with a circular arc groove, and the circular arc groove is composed of 6 segmented circular arc grooves 3 distributed along the circumference and concentric with equal diameters, ...
Embodiment 2
[0037] refer to figure 2 , image 3 , Figure 4 , the difference between this embodiment and Embodiment 1 is that: the end surface of the driven wheel gear body 2-2 close to the root of the driven wheel gear tooth 2-1 is provided with two circular arc grooves, which are respectively inner ring arc grooves and The arc grooves of the outer ring, the segments of the arc grooves of the inner ring and the segments of the arc grooves of the outer ring are staggered; the segmented arc grooves 3 are filled with plastic. All the other are with embodiment 1.
Embodiment 3
[0039] The difference between this embodiment and Embodiment 1 is that: the end surface of the driven wheel gear body 2-2 near the root of the driven wheel gear teeth 2-1 is provided with three circular arc grooves, which are respectively the first circular arc groove and the second circular arc groove. The second circle of arc grooves and the third circle of arc grooves, the segments of the first circle of arc grooves, the second circle of arc grooves and the third circle of arc grooves are staggered from each other; the segmental arc grooves 3 are filled with lead . All the other are with embodiment 1.
PUM
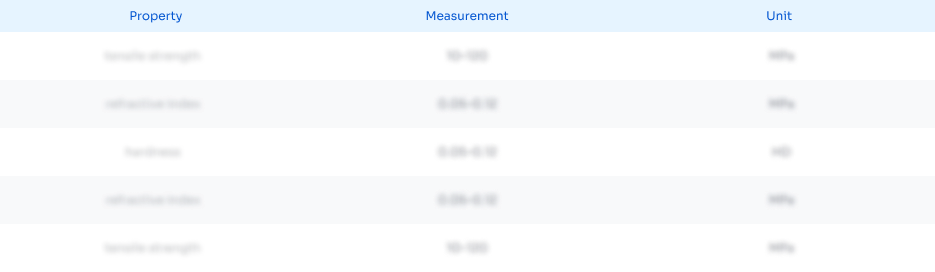
Abstract
Description
Claims
Application Information

- Generate Ideas
- Intellectual Property
- Life Sciences
- Materials
- Tech Scout
- Unparalleled Data Quality
- Higher Quality Content
- 60% Fewer Hallucinations
Browse by: Latest US Patents, China's latest patents, Technical Efficacy Thesaurus, Application Domain, Technology Topic, Popular Technical Reports.
© 2025 PatSnap. All rights reserved.Legal|Privacy policy|Modern Slavery Act Transparency Statement|Sitemap|About US| Contact US: help@patsnap.com