Method for separating and recycling tungsten in alkaline sodium tungstate solution with high chlorine content
A separation and recovery, high-chlorine alkaline technology, applied in chemical instruments and methods, tungsten compounds, alkali metal chlorides, etc., can solve the problems of affecting the ion exchange process and cannot be applied to ion exchange recovery, etc., and achieves simple process and easy operation. , the effect of high recovery rate
- Summary
- Abstract
- Description
- Claims
- Application Information
AI Technical Summary
Problems solved by technology
Method used
Image
Examples
Embodiment 1
[0028] Analysis and detection steps: Sampling the sodium perchlortungstate leaching solution, and analyzing and detecting the content of each element in it, the detection results are: Cu4.0mg / L, Ni1.4mg / L, Co2.0mg / L, Mn0.9mg / L, Zn3.6mg / L, Fe0.9mg / L, Ca0.9mg / L, Mg0.8mg / L, Al1.9mg / L, S 2- 15mg / L, W32.5g / L, Cl - 14.8g / L and OH - 5.4g / L.
[0029] Tungsten sinking step: take 5000mL sodium tungstate perchlorate solution, adjust the pH of sodium tungstate solution to 9 with hydrochloric acid, and carry out tungsten sinking with saturated calcium chloride solution, the amount of calcium chloride is CaCl 2 : W=1.15:1 (molar ratio), the temperature is 80°C, and the time is 3 hours to obtain calcium tungstate precipitation and tungsten precipitation mother liquor.
[0030] Concentration and crystallization step: adjust the pH of the tungsten sinking mother liquor obtained in the tungsten sinking step to 7 with hydrochloric acid, and concentrate the solution to obtain pure sodium chlo...
Embodiment 2
[0035] Analysis and detection steps: Sampling the sodium perchlortungstate leaching solution, and analyzing and detecting the content of each element in it, the detection results are: Cu12.0mg / L, Ni7.5.mg / L, Co0.5mg / L, Mn0 .3mg / L, Zn4.2mg / L, Fe0.7mg / L, Ca1.1mg / L, Mg1.0mg / L, Al1.7mg / L, S 2- 20mg / L, W40.9g / L, Cl - 12.0g / L and OH - 16.4g / L.
[0036] Tungsten sinking step: take 5000mL sodium perchlortungstate solution, adjust the pH of the sodium tungstate solution to 13 with hydrochloric acid, and carry out tungsten sinking with saturated calcium chloride solution, the amount of calcium chloride is CaCl 2 : W=1.25:1 (molar ratio), the temperature is 65°C, and the time is 4h, to obtain calcium tungstate precipitation and tungsten precipitation mother liquor.
[0037] Concentration and crystallization step: adjust the pH of the tungsten sinking mother liquor obtained in the tungsten sinking step to 7 with hydrochloric acid, and concentrate the solution to obtain pure sodium chlo...
Embodiment 3
[0042] Analysis and detection steps: Sampling the sodium perchlortungstate leaching solution, and analyzing and detecting the content of each element in it, the detection results are: Cu15.0mg / L, Ni6.4.mg / L, Co3.1mg / L, Mn0 .5mg / L, Zn2.6mg / L, Fe1.5mg / L, Ca3.4mg / L, Mg0.5mg / L, Al2.5mg / L, S 2- 25mg / L, W29.1g / L and Cl - 17.5g / L, OH - 10.1g / L.
[0043] Tungsten sinking step: take 5000mL sodium perchlortungstate solution, adjust the pH of the sodium tungstate solution to 13 with hydrochloric acid, and carry out tungsten sinking with saturated calcium chloride solution, the amount of calcium chloride is CaCl 2 : W=1.15:1 (molar ratio), the temperature is 80°C, and the time is 3 hours to obtain calcium tungstate precipitation and tungsten precipitation mother liquor.
[0044] Concentration and crystallization step: adjust the pH of the tungsten sinking mother liquor obtained in the tungsten sinking step to 7 with hydrochloric acid, and concentrate the solution to obtain pure sodium ...
PUM
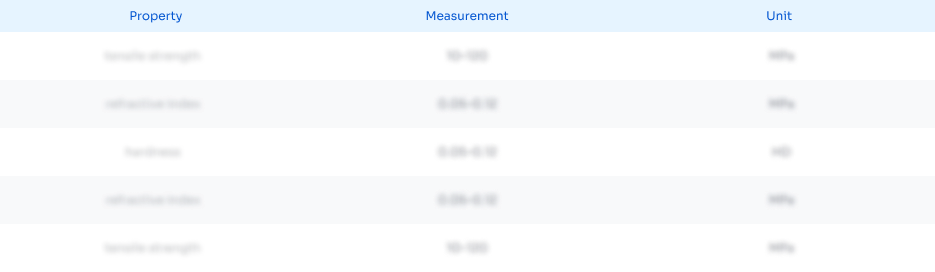
Abstract
Description
Claims
Application Information

- Generate Ideas
- Intellectual Property
- Life Sciences
- Materials
- Tech Scout
- Unparalleled Data Quality
- Higher Quality Content
- 60% Fewer Hallucinations
Browse by: Latest US Patents, China's latest patents, Technical Efficacy Thesaurus, Application Domain, Technology Topic, Popular Technical Reports.
© 2025 PatSnap. All rights reserved.Legal|Privacy policy|Modern Slavery Act Transparency Statement|Sitemap|About US| Contact US: help@patsnap.com