A connection method based on laser additive manufacturing assisted by electromagnetic induction synchronous preheating
An electromagnetic induction and connection method technology, applied in the field of material processing engineering, can solve problems such as crack sensitivity, low laser utilization rate, and large cracks, and achieve the effects of improving microstructure, improving low laser absorption rate, and improving performance
- Summary
- Abstract
- Description
- Claims
- Application Information
AI Technical Summary
Problems solved by technology
Method used
Image
Examples
specific Embodiment approach 1
[0020] Specific implementation mode one: a kind of electromagnetic induction synchronous preheating assisted connection method based on laser additive manufacturing in this embodiment, it is to carry out according to the following content:
[0021] Step 1: Process the position of the workpiece to be welded into a V-shaped groove, and clean and polish the surface of the groove and nearby positions, and fix the workpiece to be welded on the workbench with a fixture;
[0022] Step 2: Set process parameters:
[0023] Preheating part:
[0024] The induction current is 300A~1000A, the control preheating temperature is 100℃~200℃, and the distance d between the center of the induction coil and the center of the laser spot is 5mm~18mm;
[0025] Welding part:
[0026] The laser power is 300W~4000W, the spot diameter is 1mm~4mm, the welding speed is 3mm / s~40mm / s, the powder feeding speed is 2g / min~25g / min, the powder feeding carrier gas flow rate is 3L / min~12L / min , the shielding gas ...
specific Embodiment approach 2
[0029] Specific embodiment 2: The difference between this embodiment and specific embodiment 1 is that the process parameters of the preheating part are: the induction current is 500A-1000A, the control preheating temperature is 120°C-200°C, the center of the induction coil and the center of the laser spot The distance d is 8 mm to 18 mm. Others are the same as in the first embodiment.
specific Embodiment approach 3
[0030] Embodiment 3: The difference between this embodiment and Embodiment 1 is that the process parameters of the preheating part are: the induction current is 800A-1000A, the control preheating temperature is 150°C-200°C, the center of the induction coil and the center of the laser spot The distance d is 10 mm to 18 mm. Others are the same as in the first embodiment.
PUM
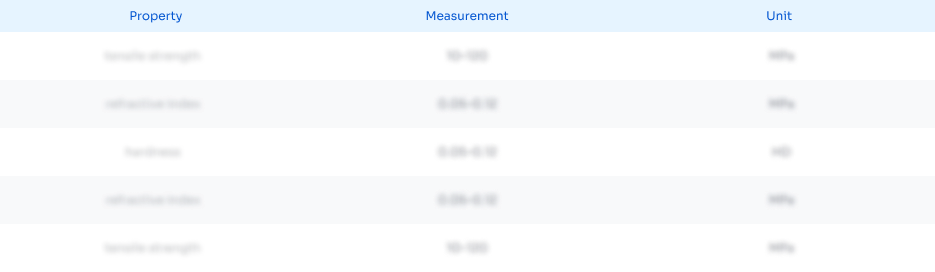
Abstract
Description
Claims
Application Information

- R&D
- Intellectual Property
- Life Sciences
- Materials
- Tech Scout
- Unparalleled Data Quality
- Higher Quality Content
- 60% Fewer Hallucinations
Browse by: Latest US Patents, China's latest patents, Technical Efficacy Thesaurus, Application Domain, Technology Topic, Popular Technical Reports.
© 2025 PatSnap. All rights reserved.Legal|Privacy policy|Modern Slavery Act Transparency Statement|Sitemap|About US| Contact US: help@patsnap.com