Continuous casting and rolling production line of wire rods and production method of production line
A technology of continuous casting, continuous rolling and production methods, which is applied in the direction of metal rolling, etc., can solve the problems of low working speed of the transport roller table, low pulling speed of the continuous casting machine, and long duration, so as to reduce the construction cost and operation and maintenance. Cost, reduction of conveying time and temperature loss, effect of uniform temperature gradient distribution
- Summary
- Abstract
- Description
- Claims
- Application Information
AI Technical Summary
Problems solved by technology
Method used
Image
Examples
Embodiment Construction
[0025] The preferred embodiments of the present invention will be described in detail below with reference to the accompanying drawings.
[0026] As shown in the figure, the wire and bar continuous casting and rolling production line in the present invention includes a continuous casting machine, a parallel flow device 8 and a rolling mill unit. The continuous casting machine is mainly composed of a rotary table 1, a ladle 2, a middle Package 3, crystallizer 4, secondary cooling section 5, tension leveler 6, cutting machine 7 and transport roller table 9, the rolling unit is mainly composed of rough rolling mill 10, middle rolling mill 12 and The finishing mill 14 is composed of 1# flying shear 11 between the rough rolling mill 10 and the middle rolling mill 12, 2# flying shear 13 between the middle rolling mill 12 and the finishing mill 14, and the parallel flow device 8 is arranged on the cutting machine 7 and rough rolling mill 10 between.
[0027] Specifically, the contin...
PUM
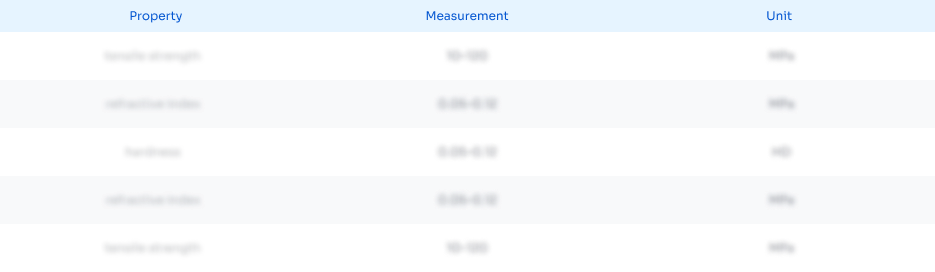
Abstract
Description
Claims
Application Information

- R&D
- Intellectual Property
- Life Sciences
- Materials
- Tech Scout
- Unparalleled Data Quality
- Higher Quality Content
- 60% Fewer Hallucinations
Browse by: Latest US Patents, China's latest patents, Technical Efficacy Thesaurus, Application Domain, Technology Topic, Popular Technical Reports.
© 2025 PatSnap. All rights reserved.Legal|Privacy policy|Modern Slavery Act Transparency Statement|Sitemap|About US| Contact US: help@patsnap.com