Catalyst for preparing 1,3-butadiene through ethanol condensation, preparation method of catalyst and application of catalyst
A catalyst and butadiene technology, applied in chemical instruments and methods, heterogeneous catalyst chemical elements, physical/chemical process catalysts, etc., can solve the problem of poor crystallization performance affecting catalytic performance, single catalyst components, and lack of active components and other problems, to achieve the effect of easy industrial scale-up, low cost and simple preparation method
- Summary
- Abstract
- Description
- Claims
- Application Information
AI Technical Summary
Problems solved by technology
Method used
Examples
Embodiment 1
[0041] 1. Add Cu(NO 3 ) 2 ·3H 2 O, Mg(NO 3 ) 2 ·6H 2 O, Al(NO 3 ) 3 9H 2 O was made into a (0.5M, 1000ml) solution in a molar ratio of (Cu / Mg / Al=0.175 / 0.375 / 0.45), and the template agent F127 (F127 was 1% W / V) A solution was added.
[0042] 2. Na 2 CO 3 and NaOH (Na 2 CO 3 (1M)+NaOH(2M)) mixed solution B, about 800ml, requires (CO 3 2- / Al 3+ =3).
[0043] 3. At 80°C, add A and B dropwise to 1000ml of water at the same time, and adjust the pH to 9 with 2M NaOH solution.
[0044] 4. The aging time is 3 hours, and it is placed overnight at room temperature, and the obtained precipitate is filtered and washed with deionized water until the pH is 7.
[0045] 5. Vacuum dry at 60°C for 12 hours.
[0046] 6. Heat treatment at 500° C. for 5 hours in an air atmosphere to obtain sample 1, wherein the atomic percentage of Cu / Mg / Al=14.98 / 37.21 / 47.81.
[0047] 7. Put 1.5 ml of the catalyst prepared above into a reaction tube, and fill the upper and lower sides of the reac...
Embodiment 2
[0050] 1. Add Cu(NO 3 ) 2 ·3H 2 O, Mg(NO 3 ) 2 ·6H 2 O, Al(NO 3 ) 3 9H 2 O was made into a (0.5M, 1000ml) solution in a molar ratio of (Cu / Mg / Al=0.175 / 0.375 / 0.45), and the template agent F127 (F127 was 3% W / V) A solution was added.
[0051] 2. Na 2 CO 3 and NaOH (Na 2 CO 3 (1.5M)+NaOH(3M)) mixed solution B, about 800ml, requires (CO 3 2- / Al 3+ = 3.75).
[0052] 3. At 80°C, add A and B dropwise to 1000ml of water at the same time, and adjust the pH to 10 with 3M NaOH solution.
[0053] Steps 4-6 are the same as in Example 1 to obtain sample 2, wherein the atomic percentage of Cu / Mg / Al==15.03 / 37.86 / 47.11.
[0054] 7. Put 1.5 ml of the catalyst prepared above into a reaction tube, and fill the upper and lower sides of the reaction tube with quartz sand. Inject 3700ml / ml cat h -1 Nitrogen, at 500 ° C for 6 hours, then lowered to 350 ° C, with a space velocity of 3900ml / ml cat h -1 The hydrogen was reduced for 3 hours, the temperature was lowered to the reacti...
Embodiment 3
[0057] 1. Add Cu(NO 3 ) 2 ·3H 2 O, Mg(NO 3 ) 2 ·6H 2 O, Al(NO 3 ) 3 9H 2 O was made into a (0.5M, 1000ml) solution in a molar ratio of (Cu / Mg / Al=0.175 / 0.375 / 0.45), and the template agent F127 (F127 was 7% W / V) A solution was added.
[0058] 2. Na 2 CO 3 and NaOH (Na 2 CO 3 (2M)+NaOH(4M)) mixed solution B, about 800ml, requires (CO 3 2- / Al 3+ =5).
[0059] 3. At 80°C, add A and B dropwise to 1000ml of water at the same time, and adjust the pH to 11 with 4M NaOH solution.
[0060] Step 4-5 is the same as embodiment 1.
[0061] 6. Heat treatment at 500° C. for 6 hours in an air atmosphere to obtain sample 3, wherein the atomic percentage of Cu / Mg / Al=15.9 / 36.72 / 47.38.
[0062] 7. Put 1.5 ml of the catalyst prepared above into a reaction tube, and fill the upper and lower sides of the reaction tube with quartz sand. Inject 4000ml / ml cat h -1 Nitrogen, keep warm at 420°C for 3h, then drop to 320°C, and use a space velocity of 4200ml / ml cat h -1The hydrogen was...
PUM
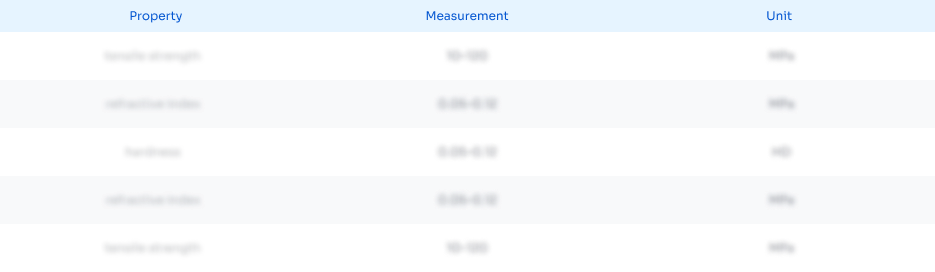
Abstract
Description
Claims
Application Information

- R&D
- Intellectual Property
- Life Sciences
- Materials
- Tech Scout
- Unparalleled Data Quality
- Higher Quality Content
- 60% Fewer Hallucinations
Browse by: Latest US Patents, China's latest patents, Technical Efficacy Thesaurus, Application Domain, Technology Topic, Popular Technical Reports.
© 2025 PatSnap. All rights reserved.Legal|Privacy policy|Modern Slavery Act Transparency Statement|Sitemap|About US| Contact US: help@patsnap.com