Method for separating and purifying lime kiln tail gas
A lime kiln and tail gas technology, applied in the chemical industry, can solve problems such as pollution, reduce investment and be beneficial to popularization and application.
- Summary
- Abstract
- Description
- Claims
- Application Information
AI Technical Summary
Problems solved by technology
Method used
Image
Examples
Embodiment 1
[0046] The method for separating and purifying lime kiln tail gas comprises the following steps:
[0047] (1) A single gas-fired lime kiln with a daily output of 600 tons of lime, with a tail gas emission of 55,000 Nm 3 / h, the tail gas temperature is 150°C, and the pressure is 4000PaG; it will contain 35% CO 2 , 55%N 2 , 8%H 2 O, 2% O 2 , Dust 30mg / Nm 3 and trace amounts of CO and SO 2 The high-temperature tail gas is passed into the water washing tower for spraying, and the sprayed tail gas is passed into the desulfurization tower for desulfurization treatment;
[0048] (2) The tail gas after desulfurization is passed into the MEA absorption tower, and the monoethanolamine solution in the MEA absorption tower absorbs the carbon dioxide in the tail gas, and the monoethanolamine solution after absorbing carbon dioxide is sent to the analysis tower, and the carbon dioxide is released after expansion and decompression ;
[0049] (3) The released carbon dioxide is pressuri...
Embodiment 2
[0052] The method for separating and purifying lime kiln tail gas comprises the following steps:
[0053] (1) A single gas-fired lime kiln with a daily output of 150 tons of lime, with a tail gas emission of 40,000Nm 3 / h, the tail gas temperature is 130°C, and the pressure is 4000PaG; it will contain 28% CO 2 , 60%N 2 , 8%H 2 O, 4% O 2 , Dust 30mg / Nm 3 and trace amounts of CO and SO 2 The high-temperature tail gas is passed into the water washing tower for spraying, and the sprayed tail gas is passed into the desulfurization tower for desulfurization treatment;
[0054] (2) The tail gas after desulfurization is passed into the MEA absorption tower, and the monoethanolamine solution in the MEA absorption tower absorbs the carbon dioxide in the tail gas, and the monoethanolamine solution after absorbing carbon dioxide is sent to the analysis tower, and the carbon dioxide is released after expansion and decompression ;
[0055] (3) The released carbon dioxide is pressuriz...
PUM
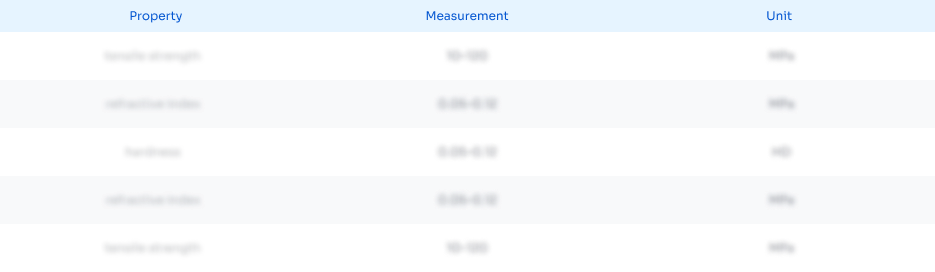
Abstract
Description
Claims
Application Information

- R&D
- Intellectual Property
- Life Sciences
- Materials
- Tech Scout
- Unparalleled Data Quality
- Higher Quality Content
- 60% Fewer Hallucinations
Browse by: Latest US Patents, China's latest patents, Technical Efficacy Thesaurus, Application Domain, Technology Topic, Popular Technical Reports.
© 2025 PatSnap. All rights reserved.Legal|Privacy policy|Modern Slavery Act Transparency Statement|Sitemap|About US| Contact US: help@patsnap.com