Die spraying system
A mold and spraying amount technology, applied in the field of die-casting spraying, can solve the problems of high rate of indifferent and unqualified products, reduce the service life of die-casting molds, and increase the number of unqualified products, so as to reduce the number of unqualified products, increase the qualified rate of products, and improve The effect of production efficiency
- Summary
- Abstract
- Description
- Claims
- Application Information
AI Technical Summary
Problems solved by technology
Method used
Image
Examples
Embodiment Construction
[0036] The present invention will be described in further detail below by means of specific embodiments:
[0037] as attached figure 1 The mold spraying system shown: includes PLC control module, man-machine interface, die-casting machine working state input module, spraying robot module, mold spraying flow control module and mold cooling water control module. Man-machine interface and PLC control module one-way communication connection, die-casting machine working status input module and PLC control module one-way communication, spraying robot module and PLC control module two-way communication, mold spraying flow control module and PLC control module one-way communication, mold The cooling water control module communicates one-way with the PLC control module.
[0038] The PLC control module of this embodiment includes a die-casting machine working state detection part, a die-casting machine abnormal judgment part, a spraying amount calculation part, a cooling water flow cal...
PUM
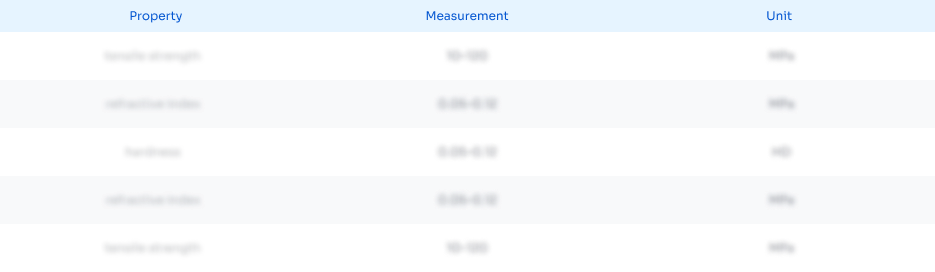
Abstract
Description
Claims
Application Information

- R&D
- Intellectual Property
- Life Sciences
- Materials
- Tech Scout
- Unparalleled Data Quality
- Higher Quality Content
- 60% Fewer Hallucinations
Browse by: Latest US Patents, China's latest patents, Technical Efficacy Thesaurus, Application Domain, Technology Topic, Popular Technical Reports.
© 2025 PatSnap. All rights reserved.Legal|Privacy policy|Modern Slavery Act Transparency Statement|Sitemap|About US| Contact US: help@patsnap.com