Method for preventing generation of center line cracks in steel board continuous casting process
A technology of continuous casting process and control center, which is applied in the field of metallurgical technology, can solve the problems of not pointing out continuous casting and rolling production, not eliminating center line cracks, and not reducing other cracks, etc., to achieve large water spray coverage, reduce molten steel flow, Uniform cooling effect
- Summary
- Abstract
- Description
- Claims
- Application Information
AI Technical Summary
Problems solved by technology
Method used
Image
Examples
Embodiment 1
[0046] The raw material of molten steel used in this example is a group of 10 furnaces of Q235B ordinary carbon steel molten steel. The size of the cast slab produced is 1500mm*230mm*long. Carry out desulfurization treatment to ensure that the S content of molten iron entering the converter is 0.018wt%, and fully remove slag; adopt top-bottom composite blowing smelting for molten iron in the converter to ensure that the P content of molten steel is 0.018wt%, and the C content is 0.08wt% .
[0047] Before continuous casting of molten steel, inspect the atomizing nozzles in the fan-shaped section and find that there is no blockage in the foot roll section and zero section atomizing nozzles, the number of blocked atomizing nozzles in the arc section is 2, the number of blocked atomizing nozzles in the horizontal section is 4, and the water supply There are no leaks in the pipeline.
[0048] During continuous casting of molten steel, turn on the high-pressure water source, and sp...
Embodiment 2
[0052] The raw material of molten steel used in this example is a group of 12 heats of Stb32 low-carbon aluminum killed steel, and the size of the cast slab produced is 1820mm*230mm*long; Desulfurization treatment is carried out before the furnace to ensure that the S content of the molten iron entering the converter is 0.008wt%, and the slag is fully removed; the molten iron is smelted by top-bottom composite blowing in the converter to ensure that the P content of the molten steel is 0.008wt%, and the C content is 0.05wt% %.
[0053] Before continuous casting of molten steel, check the atomizing nozzles in the fan-shaped section for inspection. It is found that there is no blockage in the foot roll section and the zero section atomizing nozzles, the number of blocked atomizing nozzles in the arc section is 1, and the number of blocked atomizing nozzles in the horizontal section is 3. There are no leaks in the pipeline.
[0054] During continuous casting of molten steel, turn ...
Embodiment 3
[0058] The raw material of molten steel used in this example is a group of 12 heats of Stb32 low-carbon aluminum killed steel, and the size of the cast slab produced is 1820mm*230mm*long; Desulfurization treatment is carried out before the furnace to ensure that the S content of the molten iron entering the converter is 0.012wt%, and the slag is fully removed; the molten iron is smelted by top-bottom composite blowing in the converter to ensure that the P content of the molten steel is 0.012wt%, and the C content is 0.06wt. %.
[0059] Before continuous casting of molten steel, check the atomizing nozzles in the fan-shaped section for inspection. It is found that there is no blockage in the foot roll section and the zero section atomizing nozzles, the number of blocked atomizing nozzles in the arc section is 0, the number of blocked atomizing nozzles in the horizontal section is 2, and the water supply There are no leaks in the pipeline.
[0060] During continuous casting of ...
PUM
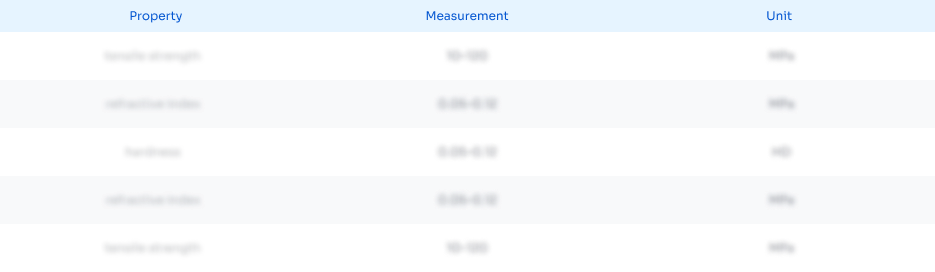
Abstract
Description
Claims
Application Information

- Generate Ideas
- Intellectual Property
- Life Sciences
- Materials
- Tech Scout
- Unparalleled Data Quality
- Higher Quality Content
- 60% Fewer Hallucinations
Browse by: Latest US Patents, China's latest patents, Technical Efficacy Thesaurus, Application Domain, Technology Topic, Popular Technical Reports.
© 2025 PatSnap. All rights reserved.Legal|Privacy policy|Modern Slavery Act Transparency Statement|Sitemap|About US| Contact US: help@patsnap.com