Acid bath process for glass paper production
A cellophane and acid bath technology, applied in the field of viscose fiber, can solve the problems of high energy consumption, small processing capacity, small equipment capacity, etc., and achieve the effects of reducing investment, reducing ends, and reducing operation and maintenance personnel.
- Summary
- Abstract
- Description
- Claims
- Application Information
AI Technical Summary
Problems solved by technology
Method used
Image
Examples
Embodiment 1
[0017] The acid bath produced by cellophane in the prior art consists of: water, sodium sulfate, sulfuric acid. In the production process, the concentration of sodium sulfate is generally controlled at 220-250g / L, and the concentration of sulfuric acid is generally controlled at 145-155g / L. There are special evaporation equipment for evaporation and crystallization equipment for acid bath recovery, but due to the small processing capacity and equipment capacity, the year-on-year energy consumption is relatively high. At the same time, personnel are required to operate independently.
[0018] A kind of acid bath process for the production of cellophane of the present invention, in the production process, the acid bath of cellophane and the acid bath of viscose fiber are integrated, and described integration is the reacid (reacted acid) of cellophane and Evaporate and crystallize in the acid bath of viscose fiber to carry out acid bath recovery; then add the acid bath of quantit...
PUM
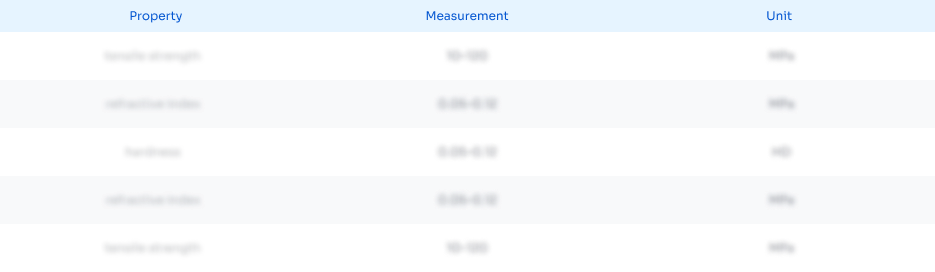
Abstract
Description
Claims
Application Information

- R&D
- Intellectual Property
- Life Sciences
- Materials
- Tech Scout
- Unparalleled Data Quality
- Higher Quality Content
- 60% Fewer Hallucinations
Browse by: Latest US Patents, China's latest patents, Technical Efficacy Thesaurus, Application Domain, Technology Topic, Popular Technical Reports.
© 2025 PatSnap. All rights reserved.Legal|Privacy policy|Modern Slavery Act Transparency Statement|Sitemap|About US| Contact US: help@patsnap.com