Blackening treatment process for surface of ironwork
A technology for blackening and iron products, applied in the direction of metal material coating process, coating, solid diffusion coating, etc., can solve the problems of air environment impact and hidden safety hazards, and achieve reasonable steps, low cost and safe operation. high sex effect
- Summary
- Abstract
- Description
- Claims
- Application Information
AI Technical Summary
Problems solved by technology
Method used
Examples
Embodiment 1
[0016] Step 1: Raise the temperature of the nitriding furnace to 625 degrees Celsius.
[0017] Step 2: Clean the surface of 110 kg of iron products without rust, oil and dirt.
[0018] Step 3: Put the cleaned iron product into the nitriding furnace.
[0019] Step 4: Add 10 milliliters of 75% alcohol solution to the nitriding furnace at a rate of 20 drops per minute for a total of 90 minutes, and a total of 900 milliliters of alcohol solution.
[0020] Step 5: Constant temperature for 120 minutes.
[0021] Step 6: Stop heating the nitriding furnace and let it cool naturally for 240 minutes. The temperature in the furnace is 400 degrees Celsius.
[0022] Step 7: Take the iron product out of the nitriding furnace and cool it down to room temperature.
PUM
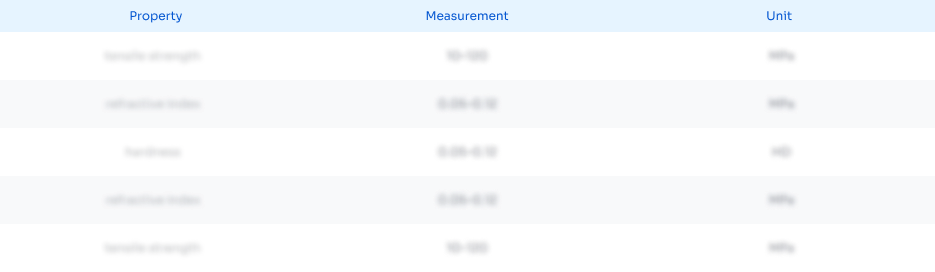
Abstract
Description
Claims
Application Information

- R&D Engineer
- R&D Manager
- IP Professional
- Industry Leading Data Capabilities
- Powerful AI technology
- Patent DNA Extraction
Browse by: Latest US Patents, China's latest patents, Technical Efficacy Thesaurus, Application Domain, Technology Topic, Popular Technical Reports.
© 2024 PatSnap. All rights reserved.Legal|Privacy policy|Modern Slavery Act Transparency Statement|Sitemap|About US| Contact US: help@patsnap.com