Preparation process for steel-cast roller
A roll and process technology, which is applied in the field of steel casting roll configuration technology, can solve problems such as spalling, increased roll manufacturing cost, and low production rate, and achieves good wear resistance and toughness, strong accident resistance, and reduced manufacturing costs. Effect
- Summary
- Abstract
- Description
- Claims
- Application Information
AI Technical Summary
Problems solved by technology
Method used
Examples
Embodiment
[0009] A configuration process for cast steel back-up rolls, wherein the material of the working layer of the back-up roll is high-alloy steel, and the core material of the roll is graphite steel; the high-alloy steel in the working layer of the roll is completely metallurgically bonded to the graphite steel at the core of the roll;
[0010] The chemical composition weight percent of the high alloy steel is: C0.5%, Si0.5%, Mn0.5-0.6%, Cr4.5%, Ni1.1%, Mo0.7%, Re0.04%, P≤0.03%, S≤0.03%, the balance is Fe;
[0011] The chemical composition weight percent of described graphite steel is: C1.5%, Si1.8%, Mn0.5%, Ni0.6%, Cr<0.2%, Mo<0.3%, P<0.03%, S<0.03 %, the balance is Fe.
PUM
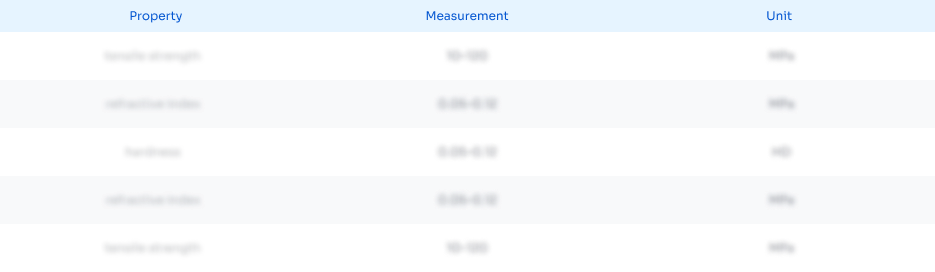
Abstract
Description
Claims
Application Information

- R&D
- Intellectual Property
- Life Sciences
- Materials
- Tech Scout
- Unparalleled Data Quality
- Higher Quality Content
- 60% Fewer Hallucinations
Browse by: Latest US Patents, China's latest patents, Technical Efficacy Thesaurus, Application Domain, Technology Topic, Popular Technical Reports.
© 2025 PatSnap. All rights reserved.Legal|Privacy policy|Modern Slavery Act Transparency Statement|Sitemap|About US| Contact US: help@patsnap.com