Coal-sludge co-combustion system based on high-temperature smoke drying and pneumatic conveying
A high-temperature flue gas and pneumatic conveying technology, used in dehydration/drying/concentrated sludge treatment, combustion methods, combustion equipment, etc., can solve the problems of complex system process, poor sealing performance of belt conveying system, and large floor space. To achieve the effect of system simplicity
- Summary
- Abstract
- Description
- Claims
- Application Information
AI Technical Summary
Problems solved by technology
Method used
Image
Examples
Embodiment Construction
[0018] The present invention will be further described below in conjunction with the accompanying drawings and embodiments.
[0019] Such as figure 1 As shown, the coal-sludge co-combustion system based on high-temperature flue gas drying and pneumatic conveying of the present invention includes a sludge storage bin 1, a screw pump 2, a spray drying pipe 3, a rotary feeder-4, and a cyclone separator 5. Rotary feeder 2 6. Roots blower 7. Jet feeder 8. Cooling condenser 9. Exhaust air fan 10. Circulating fluidized bed boiler 11. Coal hopper 12. Coal feeder 13. Limestone bin 14 , Rotary feeder three 15, dust collector 16, desulfurization device 17, induced draft fan 18 and chimney 19.
[0020] The outlet of coal feeder 12 is connected to coal feeder 13, the outlet of coal feeder 13 is connected to circulating fluidized bed boiler 11, and the outlet of circulating fluidized bed boiler 11 is connected to dust collector 16, desulfurization device 17, induced draft fan 18, chimney ...
PUM
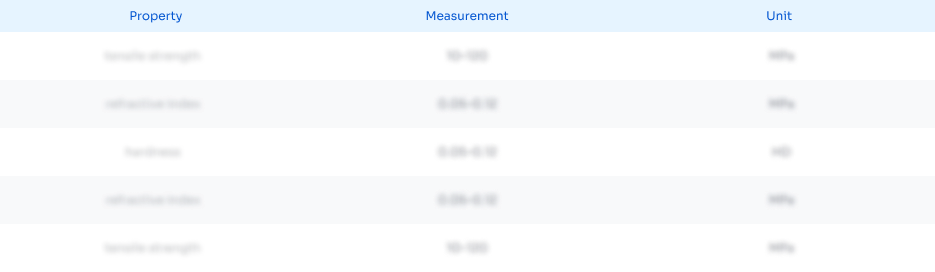
Abstract
Description
Claims
Application Information

- Generate Ideas
- Intellectual Property
- Life Sciences
- Materials
- Tech Scout
- Unparalleled Data Quality
- Higher Quality Content
- 60% Fewer Hallucinations
Browse by: Latest US Patents, China's latest patents, Technical Efficacy Thesaurus, Application Domain, Technology Topic, Popular Technical Reports.
© 2025 PatSnap. All rights reserved.Legal|Privacy policy|Modern Slavery Act Transparency Statement|Sitemap|About US| Contact US: help@patsnap.com