Continuous epichlorohydrin production method
A technology of epichlorohydrin and chloropropene, which is applied in organic chemistry and other fields, and can solve problems such as low utilization rate of raw materials, easy decomposition of peroxide when heated, and explosion hazard
- Summary
- Abstract
- Description
- Claims
- Application Information
AI Technical Summary
Problems solved by technology
Method used
Image
Examples
Embodiment 1
[0042] use figure 1 As shown in the flow process, 2 reactors are used in series, and the fresh chloropropene with a flow rate of 1.7 kg / h is mixed with a homogeneous molybdenum-based catalyst with a flow rate of 3.3 g / h, and enters from the top of the reactor 1. From reaction 2 kettle discharge V2 ', split out 30% and flow be after the ethylbenzene solution that contains 50% ethylbenzene hydroperoxide mixes at 2 kilograms / hour, be divided into 2 equal parts, from reactor 1 and reactor 2 respectively Top entry to enter.
[0043] The weight ratio of molybdenum to ethylbenzene hydroperoxide is 0.00005, epichlorohydrin: ethylbenzene hydroperoxide=3 (molar ratio).
[0044] The reaction temperature of the reactor 1 is 30° C., the reaction pressure is 0.1 MPa, and the conversion rate of ethylbenzene hydroperoxide is 50%.
[0045] The reaction temperature of the reactor 2 is 50° C., the reaction pressure is 0.1 MPa, and the conversion rate of ethylbenzene hydroperoxide is 100%.
[...
Embodiment 2
[0048] use figure 1 As shown in the flow process, 4 reactors are used in series, and the fresh chloropropene with a flow rate of 2.5 kg / h is mixed with a homogeneous molybdenum-based catalyst with a flow rate of 6.7 g / h, and enters the reactor from the top of the reactor 1. Discharge V from the last reactor 4 After splitting out 40% with flow rate and containing the cumene solution of 50% cumene hydroperoxide at 2 kilograms / hour, be divided into 4 equal parts, enter from the top inlet of reactor 1 to reactor 4 respectively.
[0049] The weight ratio of molybdenum and cumene hydroperoxide is 0.0001, and allyl chloride: cumene hydroperoxide=5 (mol ratio).
[0050] The reaction temperature of the reactor 1 is 30° C., the reaction pressure is 0.3 MPa, and the conversion rate of cumene hydroperoxide is 30%.
[0051] The reaction temperature of the reactor 2 is 40° C., the reaction pressure is 0.3 MPa, and the conversion rate of cumene hydroperoxide is 60%.
[0052] The reaction ...
Embodiment 3
[0056] use figure 1 Shown flow process, 5 reactors are used in series, and flow rate is that the fresh allyl chloride of 3.92 kg / hour is mixed with the homogeneous molybdenum-based catalyst that flow rate is 20 g / hour, enters from reactor 1 top. Discharge V from the last reactor 5 After splitting out 50% with flow rate and containing the ethylbenzene solution of 50% ethylbenzene hydroperoxide in ', be divided into 5 equal parts, enter from the top inlet of reactor 1 to reactor 5 respectively.
[0057] The weight ratio of molybdenum to ethylbenzene hydroperoxide is 0.0003, and allyl chloride: ethylbenzene hydroperoxide=7 (molar ratio).
[0058] The reaction temperature of the reactor 1 is 30° C., the reaction pressure is 0.7 MPa, and the conversion rate of ethylbenzene hydroperoxide is 35%.
[0059] The reaction temperature of the reactor 2 is 50° C., the reaction pressure is 0.7 MPa, and the conversion rate of ethylbenzene hydroperoxide is 55%.
[0060] The reaction tempera...
PUM
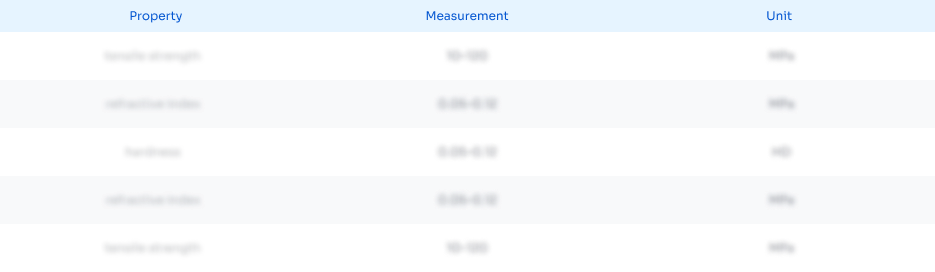
Abstract
Description
Claims
Application Information

- R&D Engineer
- R&D Manager
- IP Professional
- Industry Leading Data Capabilities
- Powerful AI technology
- Patent DNA Extraction
Browse by: Latest US Patents, China's latest patents, Technical Efficacy Thesaurus, Application Domain, Technology Topic, Popular Technical Reports.
© 2024 PatSnap. All rights reserved.Legal|Privacy policy|Modern Slavery Act Transparency Statement|Sitemap|About US| Contact US: help@patsnap.com