A three-layer co-extruded ethylene-propylene high-voltage insulating pipe busbar
A three-layer co-extrusion and high-voltage insulation technology, which is applied in the direction of insulated conductors, insulated cables, rubber insulators, etc., can solve the problems of maintenance, high frequency of maintenance, heat generation, and high requirements for busbar installation accuracy, and achieve small end surface potential and improved The effect of insulation level and field strength uniformity
- Summary
- Abstract
- Description
- Claims
- Application Information
AI Technical Summary
Problems solved by technology
Method used
Image
Examples
Embodiment 1
[0055] A preparation method of a three-layer co-extruded ethylene-propylene high-voltage insulating pipe busbar is as follows:
[0056] (1) T2 red copper is used as the material to make the main body of the tube bus with a hollow cylindrical structure;
[0057] (2) Add the raw materials of the inner screen semi-conductive layer, insulating layer and outer screen semi-conductive layer into the three hoppers of the three-layer co-extrusion extruder, start the three-layer co-extrusion extruder and simultaneously put the inner screen semi-conductive layer, The insulating layer and the outer screen semi-conductive layer are extruded to form a protective layer with an integrated structure, and the protective layer is fixed and covered on the outside of the main body of the busbar; wherein, the composition of the inner screen semi-conductive layer raw material is calculated by weight: graphite 20 parts , 11 parts of copper powder, 5.5 parts of zinc powder, 10 parts of epoxy resin, 4 ...
Embodiment 2
[0060] A preparation method of a three-layer co-extruded ethylene-propylene high-voltage insulating pipe busbar is as follows:
[0061] (1) T2 red copper is used as the material to make the main body of the tube bus with a hollow cylindrical structure;
[0062](2) Add the raw materials of the inner screen semi-conductive layer, insulating layer and outer screen semi-conductive layer into the three hoppers of the three-layer co-extrusion extruder, start the three-layer co-extrusion extruder and simultaneously put the inner screen semi-conductive layer, The insulation layer and the outer screen semi-conductive layer are extruded to form a protective layer with an integrated structure, and the protective layer is fixed and covered on the outside of the main body of the busbar; wherein, the composition of the inner screen semi-conductive layer raw material is calculated by weight: graphite 15 parts , 10 parts of copper powder, 5 parts of zinc powder, 5 parts of epoxy resin, 3 part...
Embodiment 3
[0065] A preparation method of a three-layer co-extruded ethylene-propylene high-voltage insulating pipe busbar is as follows:
[0066] (1) T2 red copper is used as the material to make the main body of the tube bus with a hollow cylindrical structure;
[0067] (2) Add the raw materials of the inner screen semi-conductive layer, insulating layer and outer screen semi-conductive layer into the three hoppers of the three-layer co-extrusion extruder, start the three-layer co-extrusion extruder and simultaneously put the inner screen semi-conductive layer, The insulation layer and the outer screen semi-conductive layer are extruded to form a protective layer with an integrated structure, and the protective layer is fixed and covered on the outside of the main body of the busbar; wherein, the composition of the inner screen semi-conductive layer raw material is calculated by weight: graphite 25 parts , 12 parts of copper powder, 6 parts of zinc powder, 15 parts of epoxy resin, 6 pa...
PUM
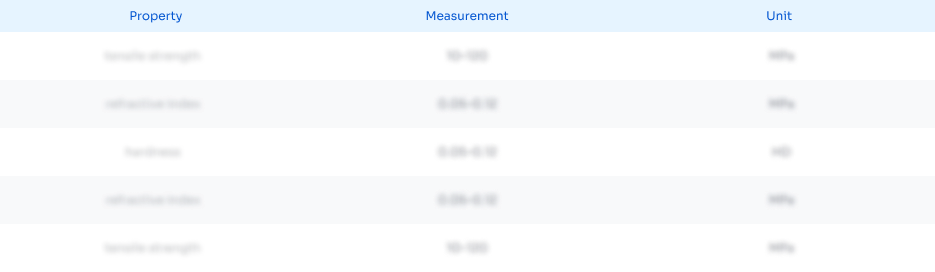
Abstract
Description
Claims
Application Information

- R&D Engineer
- R&D Manager
- IP Professional
- Industry Leading Data Capabilities
- Powerful AI technology
- Patent DNA Extraction
Browse by: Latest US Patents, China's latest patents, Technical Efficacy Thesaurus, Application Domain, Technology Topic, Popular Technical Reports.
© 2024 PatSnap. All rights reserved.Legal|Privacy policy|Modern Slavery Act Transparency Statement|Sitemap|About US| Contact US: help@patsnap.com