Method for automatically identifying defect type of polyethylene electrofusion joint through ultrasonic phased array inspection
An ultrasonic phased array, electrofusion joint technology, applied in character and pattern recognition, analysis of solids using sonic/ultrasonic/infrasonic waves, instruments, etc., can solve problems such as inability to identify, high quality requirements for ultrasonic spectra, and reduce professional requirements. , The defect identification results are reliable and the amount of data is small.
- Summary
- Abstract
- Description
- Claims
- Application Information
AI Technical Summary
Problems solved by technology
Method used
Image
Examples
specific Embodiment example 1
[0108] According to GB / T29461-2012, the ultrasonic phased array inspection is carried out on the normal and non-defective electrofusion joints, and the output ultrasonic images are as follows: figure 2 shown. Prior to the safety assessment of the EF joint according to GB / T29460-2012, defect identification is first required. The specific steps are:
[0109] (1) Digitization of ultrasound atlas. Extract the ultrasonic atlas B-scan image 2 (fixed size 407*312); establish a one-to-one correspondence between the RGB value of the image and the sound pressure intensity, and obtain the R, G, and B curves corresponding to the sound pressure intensity according to the standard color bar interpolation results, Use the linear regression method to fit the three piecewise linear functions of the corresponding curves, use the weight method to determine the calculation formula of the corresponding intensity of different pixels, and finally obtain a two-dimensional matrix; use the RGB value...
PUM
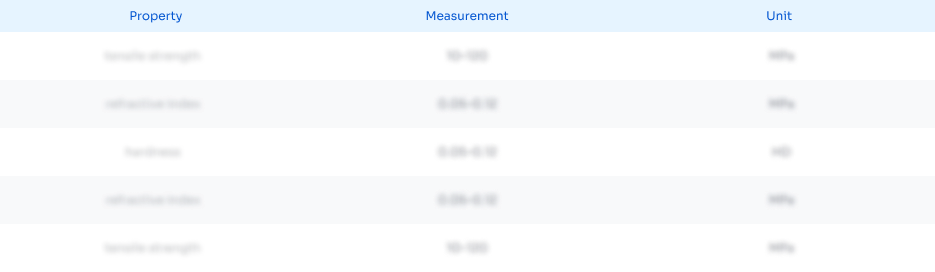
Abstract
Description
Claims
Application Information

- R&D Engineer
- R&D Manager
- IP Professional
- Industry Leading Data Capabilities
- Powerful AI technology
- Patent DNA Extraction
Browse by: Latest US Patents, China's latest patents, Technical Efficacy Thesaurus, Application Domain, Technology Topic, Popular Technical Reports.
© 2024 PatSnap. All rights reserved.Legal|Privacy policy|Modern Slavery Act Transparency Statement|Sitemap|About US| Contact US: help@patsnap.com