Tunnel kiln and combustion control method thereof
A control method and tunnel kiln technology, applied in the field of kilns, can solve the problems of uneven radiation, unfavorable convective heat transfer, low reliability and precision, etc., to improve the uniformity of temperature distribution, increase air disturbance, and improve product quality. quality effect
- Summary
- Abstract
- Description
- Claims
- Application Information
AI Technical Summary
Problems solved by technology
Method used
Image
Examples
Embodiment Construction
[0040]In order to make the object, technical solution and advantages of the present invention clearer, the present invention will be further described in detail below in conjunction with the accompanying drawings and embodiments. It should be understood that the specific embodiments described here are only used to explain the present invention, not to limit the present invention. In addition, the technical features involved in the various embodiments of the present invention described below can be combined with each other as long as they do not constitute a conflict with each other.
[0041] refer to figure 1 , according to the preferred embodiment of the present invention, a plurality of combustion chambers 4 are evenly arranged at equal distances on the kiln wall in the kiln length direction, and one or more layers can be arranged according to the height of the kiln wall during practical application. For the convenience of description in this embodiment, The simple case of ...
PUM
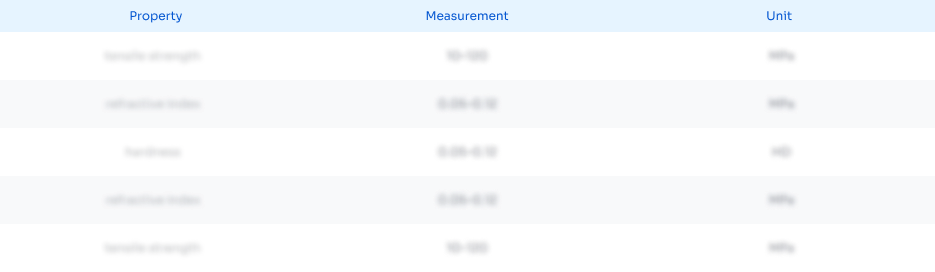
Abstract
Description
Claims
Application Information

- Generate Ideas
- Intellectual Property
- Life Sciences
- Materials
- Tech Scout
- Unparalleled Data Quality
- Higher Quality Content
- 60% Fewer Hallucinations
Browse by: Latest US Patents, China's latest patents, Technical Efficacy Thesaurus, Application Domain, Technology Topic, Popular Technical Reports.
© 2025 PatSnap. All rights reserved.Legal|Privacy policy|Modern Slavery Act Transparency Statement|Sitemap|About US| Contact US: help@patsnap.com