Crease-resistant finishing method for cellulosic fiber fabric
A cellulose fiber, anti-wrinkle finishing technology, used in fiber processing, plant fibers, textiles and papermaking, etc., can solve the problems of large loss of strength and wear resistance, stress concentration, and large loss of strength in anti-wrinkle finishing, and achieve improved strength and Large loss of wear resistance, no yellowing, and guaranteed anti-wrinkle effect
- Summary
- Abstract
- Description
- Claims
- Application Information
AI Technical Summary
Problems solved by technology
Method used
Examples
Embodiment 1
[0036] An anti-wrinkle finishing method for cellulose fiber fabrics, which uses a durable anti-wrinkle finishing agent and adopts a two-dipping and two-rolling finishing process to perform anti-wrinkle finishing on the cellulose fiber fabrics; 75-80%; pre-baking at 80-90°C for about 1-3min; baking at 120°C for 2-5min; the durable anti-wrinkle finishing agent includes the following components by weight:
[0037] Dimethylol urea resin 15
[0038] Dimethyloltriazinone 18
[0039] Methylol melamine 12
[0040] Butyl Acrylate 2
[0041] Ammonium Citrate7
[0042] Maleic acid-acrylic acid copolymer 3
[0043] Polycarboxylate 1
[0044] Fatty alcohol polyoxyethylene ether 2
[0045] Nano Titanium Dioxide 0.5
[0046] Dispersant 1
[0047] Penetrant 3;
[0048] The preparation process of the dimethylol urea resin is as follows: adding a formaldehyde solution with a mass percentage of 37-40% in a ceramic reaction kettle, adjusting the pH value of the formaldehyde solution with...
Embodiment 2
[0050] An anti-wrinkle finishing method for cellulose fiber fabrics, which uses a durable anti-wrinkle finishing agent and adopts a two-dipping and two-rolling finishing process to perform anti-wrinkle finishing on the cellulose fiber fabrics; 75-80%; pre-baking at 80-90°C for about 1-3min; baking at 180°C for 2-5min; characterized in that: the durable anti-wrinkle finishing agent includes the following components by weight:
[0051] Dimethylol urea resin 20
[0052] Dimethyloltriazinone 30
[0053] Methylol melamine 15
[0054] Butyl Acrylate 5
[0055] Ammonium Citrate 10
[0056] Maleic acid-acrylic acid copolymer 6
[0057] Polycarboxylate 1.5
[0058] Fatty alcohol polyoxyethylene ether 5
[0059] Nano Titanium Dioxide 3
[0060] Dispersant 2
[0061] Penetrant 6;
[0062]The preparation process of the dimethylol urea resin is as follows: adding a formaldehyde solution with a mass percentage of 37-40% in a ceramic reaction kettle, adjusting the pH value of the fo...
PUM
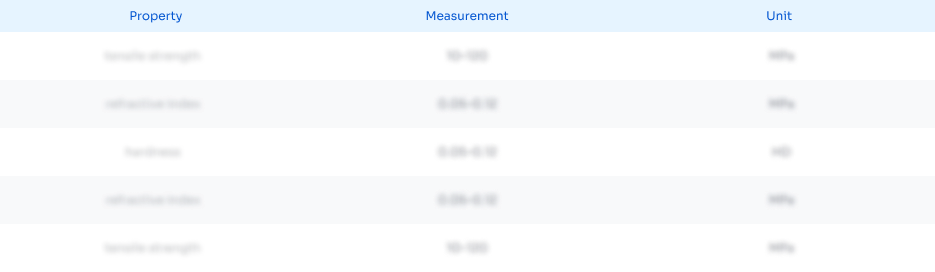
Abstract
Description
Claims
Application Information

- R&D
- Intellectual Property
- Life Sciences
- Materials
- Tech Scout
- Unparalleled Data Quality
- Higher Quality Content
- 60% Fewer Hallucinations
Browse by: Latest US Patents, China's latest patents, Technical Efficacy Thesaurus, Application Domain, Technology Topic, Popular Technical Reports.
© 2025 PatSnap. All rights reserved.Legal|Privacy policy|Modern Slavery Act Transparency Statement|Sitemap|About US| Contact US: help@patsnap.com