A kind of method that utilizes liquor lees to prepare xylose
A technology of liquor distillers grains and xylose, which is applied in the direction of sugar production, application, sugar production, etc., can solve the problems that it is not easy to use in large-scale chemical industry, xylose products are not easy to pass, and xylose solution has complex components, etc., to achieve High marketing value, preventing production technology from being feasible, and reducing process equipment and process costs
- Summary
- Abstract
- Description
- Claims
- Application Information
AI Technical Summary
Problems solved by technology
Method used
Examples
Embodiment 1
[0057] A method for preparing xylose from liquor distillers grains, comprising the following process steps:
[0058] A. Pretreatment of liquor distiller's grains
[0059] Pretreating distiller's grains of liquor to obtain pretreated distiller's grains of liquor;
[0060] B. Acid hydrolysis of liquor lees
[0061] Under the conditions of acid concentration of 0.1%, material-to-liquid mass-volume ratio of 1:3, acid hydrolysis temperature of 40°C, and acid hydrolysis time of 0.5 h, the pretreated liquor distiller's grains in step A were hydrolyzed and filtered with ultrasonic power of 120W, Obtain the acidic filtrate for subsequent use;
[0062] C. Alkaline hydrolysis of liquor distiller's grains
[0063] Under the conditions of alkali concentration of 1%, solid-liquid mass-volume ratio of 1:3, alkali hydrolysis temperature of 100°C, and alkali hydrolysis time of 1 h, the pretreated liquor distiller's grains in step A are hydrolyzed and filtered with ultrasonic waves with a po...
Embodiment 2
[0079] A method for preparing xylose from liquor distillers grains, comprising the following process steps:
[0080] A. Pretreatment of liquor distiller's grains
[0081] Pretreating distiller's grains of liquor to obtain pretreated distiller's grains of liquor;
[0082] B. Acid hydrolysis of liquor lees
[0083]The liquor distiller's grains that have been pretreated in step A are hydrolyzed and filtered with an ultrasonic wave with a power of 200W under the conditions of an acid concentration of 3%, a material-to-liquid mass-to-volume ratio of 1:30, an acid hydrolysis temperature of 100°C, and an acid hydrolysis time of 6 hours, to obtain Acidic filtrate for standby;
[0084] C. Alkaline hydrolysis of liquor distiller's grains
[0085] The liquor distiller's grains that have been pretreated in step A are hydrolyzed and filtered with an ultrasonic wave with a power of 200W under the conditions of an alkali concentration of 10%, a material-to-liquid mass-to-volume ratio of 1...
Embodiment 3
[0101] A method for preparing xylose from liquor distillers grains, comprising the following process steps:
[0102] A. Pretreatment of liquor distiller's grains
[0103] Pretreating distiller's grains of liquor to obtain pretreated distiller's grains of liquor;
[0104] B. Acid hydrolysis of liquor lees
[0105] Under the conditions of acid concentration of 1.55%, material-to-liquid mass-volume ratio of 1:16.5, acid hydrolysis temperature of 70°C, and acid hydrolysis time of 3 hours, the pretreated liquor distiller's grains in step A were hydrolyzed and filtered with ultrasonic power of 160W to obtain Acidic filtrate for standby;
[0106] C. Alkaline hydrolysis of liquor distiller's grains
[0107] Under the conditions of alkali concentration of 5.5%, material-to-liquid mass-volume ratio of 1:16.5, alkali hydrolysis temperature of 120°C, and alkali hydrolysis time of 5.5 hours, the pretreated liquor distillers grains in step A are hydrolyzed and filtered with ultrasonic po...
PUM
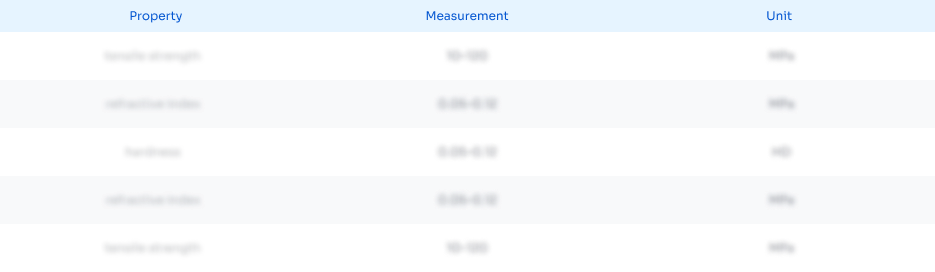
Abstract
Description
Claims
Application Information

- R&D
- Intellectual Property
- Life Sciences
- Materials
- Tech Scout
- Unparalleled Data Quality
- Higher Quality Content
- 60% Fewer Hallucinations
Browse by: Latest US Patents, China's latest patents, Technical Efficacy Thesaurus, Application Domain, Technology Topic, Popular Technical Reports.
© 2025 PatSnap. All rights reserved.Legal|Privacy policy|Modern Slavery Act Transparency Statement|Sitemap|About US| Contact US: help@patsnap.com