Machining method for aero-engine high-temperature alloy counterweight blade
An aero-engine and high-temperature alloy technology, which is applied in the processing field of aero-engine high-temperature alloy counterweight blades, can solve problems such as low processing efficiency, poor consistency, and inconsistent processing standards, so as to improve processing efficiency, reduce the number of tooling, and shorten the processing time. cycle effect
- Summary
- Abstract
- Description
- Claims
- Application Information
AI Technical Summary
Problems solved by technology
Method used
Image
Examples
Embodiment Construction
[0029] The technical solutions of the present invention will be further described below in conjunction with the accompanying drawings and through specific implementation methods.
[0030] see Figure 1 to Figure 5 As shown, in this embodiment, a method for processing a superalloy counterweight blade of an aero-engine, the counterweight blade is composed of a blade root and a blade profile 9, wherein the blade root includes: a blade root end surface 1, a steam inlet edge mortise 2 , steam outlet side mortise 3, inner arc radial surface 4, steam outlet side 5, back arc radial surface 6, steam inlet side 7, and the transition surface 8 between the blade shape and the blade root; the blank of the counterweight blade is Enveloping the block blank 9 of the blade root and the blade shape, the specific processing method of the counterweight blade is as follows:
[0031] 1. Wire cutting blade root tenon and groove: such as image 3 As shown, most of the margin of the tongue and groov...
PUM
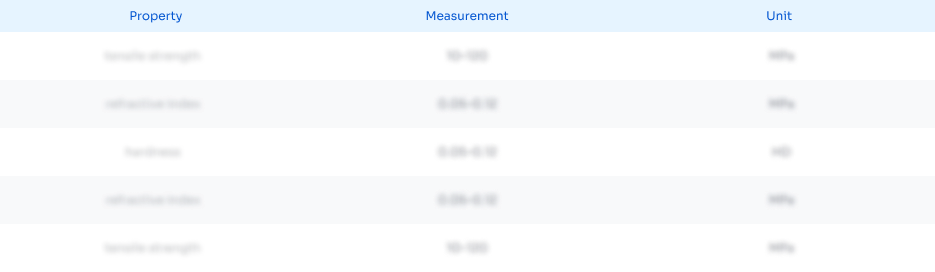
Abstract
Description
Claims
Application Information

- R&D
- Intellectual Property
- Life Sciences
- Materials
- Tech Scout
- Unparalleled Data Quality
- Higher Quality Content
- 60% Fewer Hallucinations
Browse by: Latest US Patents, China's latest patents, Technical Efficacy Thesaurus, Application Domain, Technology Topic, Popular Technical Reports.
© 2025 PatSnap. All rights reserved.Legal|Privacy policy|Modern Slavery Act Transparency Statement|Sitemap|About US| Contact US: help@patsnap.com