Cooling coating special for lost foam casting and preparation method of cooling coating
A technology of lost foam casting and coating, which is applied to casting molding equipment, coatings, casting molds, etc. It can solve the problems of high defect rate of products, and achieve the effects of suitable high temperature air permeability, scientific design, and good brushability
- Summary
- Abstract
- Description
- Claims
- Application Information
AI Technical Summary
Problems solved by technology
Method used
Examples
Embodiment 1
[0026] The special cooling coating for lost foam casting in this embodiment is made of the following raw materials in parts by weight: 25 parts of modified zircon powder, 10 parts of modified zeolite powder, 14 parts of modified attapulgite, 3 parts of modified bentonite, 20 parts of white oil, 12 parts of pumice sand, 7 parts of metakaolin, 3 parts of quicklime, 2 parts of PB2400 polyisobutylene, 2 parts of low polymerization polyvinyl alcohol, 3 parts of zinc chromate. The preparation method of the special cooling paint for lost foam casting is as follows: mix the above-mentioned raw materials evenly, add colloid mill to emulsify, and the gap between the colloid mill is 2 mm.
[0027] Described modified zircon powder is made by following steps:
[0028] (1) After sieving the zircon powder, wash it with water to remove floating dust and impurities on the surface until the pH of the washing liquid is 7-8;
[0029] (2) Mix the obtained zircon powder and phosphoric acid solutio...
Embodiment 2
[0039] The special cooling coating for lost foam casting in this embodiment is made of the following raw materials in parts by weight: 20 parts of modified zircon powder, 12 parts of modified zeolite powder, 12 parts of modified attapulgite, 4 parts of modified bentonite, 18 parts of white oil, 15 parts of pumice sand, 6 parts of metakaolin, 4 parts of quicklime, 1 part of PB2300 polyisobutylene, 3 parts of low-polymerization polyvinyl alcohol, and 2 parts of zinc chromate.
[0040] Its preparation method and each modified raw material preparation method are identical with embodiment 1.
[0041] The test method was the same as that in Example 1: the defective rate of the control group was 14‰, and the defective rate of the observation group was 2‰.
Embodiment 3
[0043] The special cooling paint for lost foam casting in this embodiment is made of the following raw materials in parts by weight: 30 parts of modified zircon powder, 9 parts of modified zeolite powder, 15 parts of modified attapulgite, 2 parts of modified bentonite, 21 parts of white oil, 7 parts of pumice sand, 8 parts of metakaolin, 2 parts of quicklime, 3 parts of PB2400 polyisobutylene, 1 part of low degree of polymerization polyvinyl alcohol, 4 parts of zinc chromate.
[0044] Its preparation method and each modified raw material preparation method are identical with embodiment 1.
[0045] The test method was the same as in Example 1: the defective rate of the control group was 14‰, and the defective rate of the observation group was 4‰.
PUM
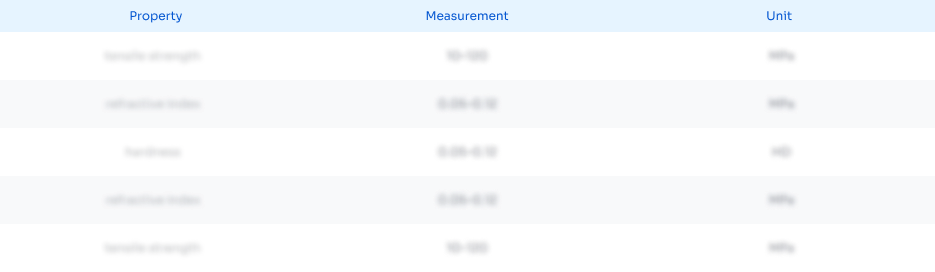
Abstract
Description
Claims
Application Information

- R&D
- Intellectual Property
- Life Sciences
- Materials
- Tech Scout
- Unparalleled Data Quality
- Higher Quality Content
- 60% Fewer Hallucinations
Browse by: Latest US Patents, China's latest patents, Technical Efficacy Thesaurus, Application Domain, Technology Topic, Popular Technical Reports.
© 2025 PatSnap. All rights reserved.Legal|Privacy policy|Modern Slavery Act Transparency Statement|Sitemap|About US| Contact US: help@patsnap.com