Preparation process of lithium iron phosphate material
A preparation process, a technology of lithium iron phosphate, applied in the direction of phosphorus compounds, structural parts, inorganic chemistry, etc., can solve the problems of difficult control of product particle size, uneven distribution, irregular morphology, etc., to improve pulping performance, improve Specific capacity, effect of increasing tap density
- Summary
- Abstract
- Description
- Claims
- Application Information
AI Technical Summary
Problems solved by technology
Method used
Image
Examples
Embodiment 1
[0012] A preparation process of lithium iron phosphate material, the following steps are carried out:
[0013] Step 1, according to mass percentage, lithium carbonate 20%, ferrous oxalate 40%, diammonium hydrogen phosphate 40%
[0014] Mixing, adding aluminum hydroxide of 0.5-1% of the total mass, putting it into a ball mill tank for ball milling for 9 hours, taking it out and placing it under the protection of argon for sintering for 12 hours, cooling for 7 hours to form a mixture;
[0015] Step 2: add 73 grams of white sugar and 1150 ml of alcohol to 1 kg of the mixture, ball mill for 8.5 hours, send to the workshop for drying, sinter at 720 ° C for 12 hours, cool and pulverize, and pass through a 100-mesh sieve.
Embodiment 2
[0017] The difference from Example 1 lies in that in step 2, pre-pressing is performed on the rollers after drying, and the gap between the rollers is 2 mm, and then sintering is performed.
[0018] According to the analysis of experimental data before and after transformation (100 batteries), this patent can increase the overall tap density by more than 30%, increase the specific surface area by about 30%, and increase the specific capacity at 0.5C by about 30%, which can effectively improve the material performance.
[0019] Some experimental reference data:
[0020] Product element content (%) and tap density
[0021] experiment number T. D (g / cm 3 ) Example 1 1.00 Example 2 1.36
[0022] specific surface area
[0023] Scheme number Example 1 Example 2 specific surface area 14.956 19.410
[0024] Directly sealed battery test results (100 batteries):
[0025]
[0026] In the present invention, adding a small amount...
PUM
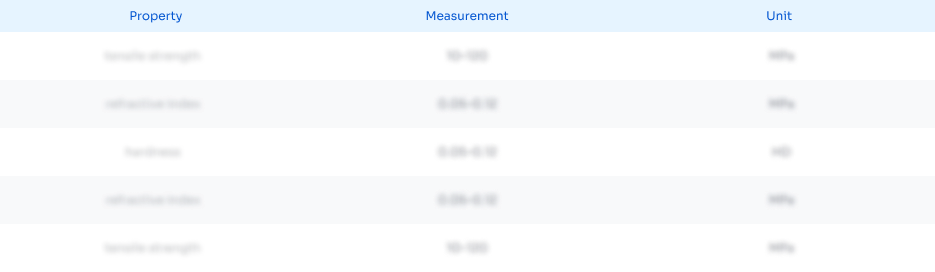
Abstract
Description
Claims
Application Information

- Generate Ideas
- Intellectual Property
- Life Sciences
- Materials
- Tech Scout
- Unparalleled Data Quality
- Higher Quality Content
- 60% Fewer Hallucinations
Browse by: Latest US Patents, China's latest patents, Technical Efficacy Thesaurus, Application Domain, Technology Topic, Popular Technical Reports.
© 2025 PatSnap. All rights reserved.Legal|Privacy policy|Modern Slavery Act Transparency Statement|Sitemap|About US| Contact US: help@patsnap.com