Extrusion manufacturing process for hub outer ring
A manufacturing process and outer ring technology, which is applied in the field of extrusion manufacturing process of the outer ring of the wheel hub, can solve the problems of high production cost, low mechanical performance, large machining allowance of metal casting wheels, etc.
- Summary
- Abstract
- Description
- Claims
- Application Information
AI Technical Summary
Problems solved by technology
Method used
Examples
Embodiment Construction
[0019] The extrusion manufacturing process of the wheel hub outer ring of the present invention comprises the following steps:
[0020] The first step is to preheat the mold, preheat the extrusion mold to 300-400°C by means of intermediate frequency heating, and turn off the intermediate frequency heating;
[0021] The second step is to close the mold and pressurize the extrusion mold. Press the aluminum alloy liquid into the extrusion mold with a pressure of 160-170 tons. 730~780℃;
[0022] The third step is to maintain the pressure, turn off the intermediate frequency heating, and continuously generate a pressure of 160-170 tons on the extrusion die, and last for 40-60 seconds;
[0023] The fourth step, the second pressurization, continues to heat the extrusion mold with intermediate frequency, the heating temperature is 500-550 °C; the pressure is 170-180 tons, and the pressurization time is 10-20 seconds;
[0024] The fifth step is to cool down with water, turn off the i...
PUM
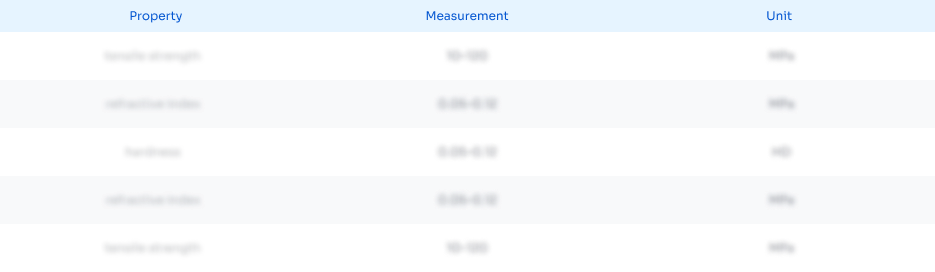
Abstract
Description
Claims
Application Information

- R&D
- Intellectual Property
- Life Sciences
- Materials
- Tech Scout
- Unparalleled Data Quality
- Higher Quality Content
- 60% Fewer Hallucinations
Browse by: Latest US Patents, China's latest patents, Technical Efficacy Thesaurus, Application Domain, Technology Topic, Popular Technical Reports.
© 2025 PatSnap. All rights reserved.Legal|Privacy policy|Modern Slavery Act Transparency Statement|Sitemap|About US| Contact US: help@patsnap.com