Imprinting material
A base material and compound technology, applied in the field of imprinting materials, can solve problems such as unusable molds, achieve high scratch resistance, and expand the effect of process margin
- Summary
- Abstract
- Description
- Claims
- Application Information
AI Technical Summary
Problems solved by technology
Method used
Image
Examples
preparation example Construction
[0119] [Preparation of Imprint Material]
[0120] The production method of the imprint material of the present invention is not particularly limited, as long as (A) component, (B) component, (C) component, and (D) component, (E) component, (F) component and The component (G) may be mixed with other desired additives to bring the imprint material into a uniform state.
[0121] In addition, there is no problem in the order of mixing the components (A) to (G) and other additives as desired, as long as a uniform imprint material can be obtained, and is not particularly limited. As its preparation method, the method of mixing (B) component in a predetermined ratio with (A) component is mentioned, for example. In addition, there may also be mentioned a method in which (C)component, (D)component, (E)component, (F)component, and (G)component are further appropriately mixed to form a uniform imprint material. Furthermore, the method of adding and mixing other additives as needed at a...
Embodiment 1
[0137] 9.9 g of KAYARAD (registered trademark) DPEA-12 (hereinafter, abbreviated as "DPEA-12" in this specification) (manufactured by Nippon Kayaku Co., Ltd.) and N,N'-dimethylacrylamide (Tokyo Chemical Industry Co., Ltd. 0.1 g of Lucirin (registered trademark) TPO (manufactured by BASF JAPAN Co., Ltd.) (hereinafter referred to as "Lucirin TPO" in this specification) 0.25 g (relative to DPEA-12, N, N The total mass of '-dimethylacrylamide is 2.5phr), and the imprint material PNI-a1 is prepared.
Embodiment 2
[0139] 9.995 g of NK Ester A-200 (hereinafter referred to simply as "A-200" in this specification) (manufactured by Shin-Nakamura Chemical Industry Co., Ltd.) and 0.005 g of N,N'-dimethylacrylamide were mixed, and the mixture was mixed with Add 0.25g of Lucirin TPO (2.5phr relative to the total mass of A-200 and N,N'-dimethylacrylamide) to prepare the imprint material PNI-a2.
PUM
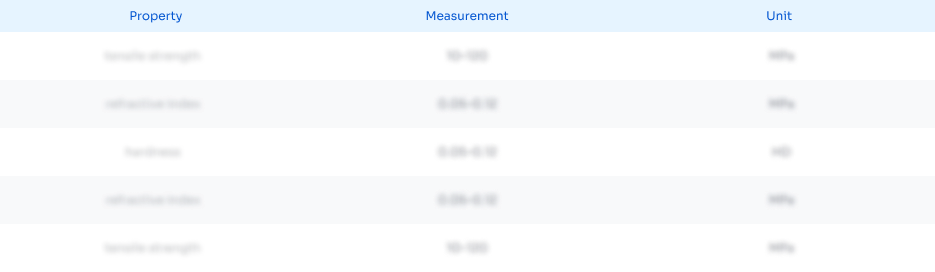
Abstract
Description
Claims
Application Information

- Generate Ideas
- Intellectual Property
- Life Sciences
- Materials
- Tech Scout
- Unparalleled Data Quality
- Higher Quality Content
- 60% Fewer Hallucinations
Browse by: Latest US Patents, China's latest patents, Technical Efficacy Thesaurus, Application Domain, Technology Topic, Popular Technical Reports.
© 2025 PatSnap. All rights reserved.Legal|Privacy policy|Modern Slavery Act Transparency Statement|Sitemap|About US| Contact US: help@patsnap.com