A Suspended Unbalanced Dynamic Tension Sensor
A tension sensor and unbalanced technology, applied in the field of sensing, can solve problems such as complex installation and disassembly, uneven force transmission, uneven tension, etc., to facilitate disassembly and installation, ensure measurement stability, and reduce human and financial resources Effect
- Summary
- Abstract
- Description
- Claims
- Application Information
AI Technical Summary
Problems solved by technology
Method used
Image
Examples
Embodiment Construction
[0043] Below in conjunction with accompanying drawing, technical scheme of the present invention is described in further detail:
[0044] The invention discloses a suspension type unbalanced dynamic tension sensor, which comprises a three-axis force-bearing body, a baffle plate, first to third nuts, first to third rollers, first to fourth strain gauges, and a rope and electrical boxes;
[0045] The triaxial force-bearing body includes a force-bearing base plate and first to third force-conducting cylinders;
[0046] The first to third rollers are chamfering rollers;
[0047] The first force-guiding cylinder and the third force-guiding cylinder are vertically arranged at both ends of the force-bearing base plate, the second force-guiding cylinder is vertically set in the middle of the force-bearing base plate, and the first to third force-guiding cylinders Chamfers corresponding to the first to third rollers are respectively provided between the stressed bottom plate;
[0048]...
PUM
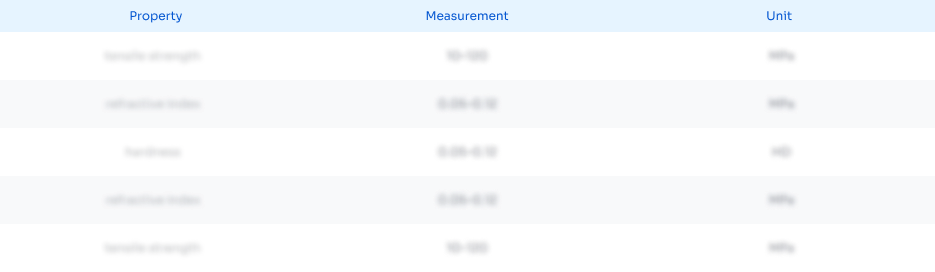
Abstract
Description
Claims
Application Information

- Generate Ideas
- Intellectual Property
- Life Sciences
- Materials
- Tech Scout
- Unparalleled Data Quality
- Higher Quality Content
- 60% Fewer Hallucinations
Browse by: Latest US Patents, China's latest patents, Technical Efficacy Thesaurus, Application Domain, Technology Topic, Popular Technical Reports.
© 2025 PatSnap. All rights reserved.Legal|Privacy policy|Modern Slavery Act Transparency Statement|Sitemap|About US| Contact US: help@patsnap.com