A kind of high vinyl polybutadiene rubber with adjustable microstructure and preparation method thereof
A technology of polybutadiene and butadiene, which is applied in the field of high vinyl polybutadiene rubber and its preparation, can solve the problems of unadjustable microstructure, reduce the molecular weight of polymerization products, reduce the viscosity of polymerization reaction glue, etc., and achieve broad The effect of market and development prospects, low cost, and good safety
- Summary
- Abstract
- Description
- Claims
- Application Information
AI Technical Summary
Problems solved by technology
Method used
Image
Examples
Embodiment 1
[0033] Under the protection of nitrogen, add MoCl to the dry catalyst reaction bottle in sequence 5 , octanol and hydrogenated gasoline, of which octanol / MoCl 5 2 / 1, react at 20°C for 48h to obtain the main catalyst MoCl for butadiene polymerization 3 (OC 8 h 17 ) 2 . In a plurality of airtight containers vacuumized and filled with nitrogen, the quantitative MoCl 3 (OC 8 h 17 ) 2 with variable AlEt 3 well mixed.
[0034] Under nitrogen protection, 30 ml of a hydrogenated gasoline solution of butadiene monomer was added to a dry and sealed 50 ml reaction flask, wherein the concentration of butadiene was 1.4 g / 10 ml. Add MoCl 3 (OC 8 h 17 ) 2 with AlEt 3 The reaction liquid, wherein the molar ratio of Mo / Bd is 2×10 -3, the polymerization was carried out at 30 °C. After 6 hours, the polymerization reaction was terminated with an ethanol solution containing 0.02 g / ml anti-aging agent 264, and the ethanol was condensed to obtain polybutadiene. The polybutadiene pr...
Embodiment 2
[0039] Prepare MoCl according to Example 1 3 (OC 8 h 17 ) 2 Catalyst, in a plurality of airtight containers that are evacuated and filled with nitrogen, variable MoCl 3 (OC 8 h 17 ) 2 with quantitative AlEt 3 Mix well, wherein the Al / Mo molar ratio is 3. Polymerization was carried out according to the polymerization method of Example 1 and the polybutadiene obtained in this example was characterized. Polymerization conditions and polymer test results are shown in Table 2.
[0040] Table 2 MoCl 3 (OC 8 h 17 ) 2 Effect of / Bd on polymer structure
[0041]
[0042] It can be seen from Table 2 that when Mo / Bd>0.8×10 -3 Finally, the conversion rate is in the range of 60% to 70%. Mo / Bd has little effect on the 1,2-structure content. With the increase of Mo / Bd, the number of active centers increases, and the molecular weight and molecular weight distribution gradually decrease.
Embodiment 3
[0044] Prepare MoCl according to Example 1 3 (OC 8 h 17 ) 2 Catalyst, in a vacuum-filled airtight container filled with nitrogen, a certain amount of MoCl 3 (OC 8 h 17 ) 2 with quantitative AlEt 3 Mix well, wherein the Al / Mo molar ratio is 3. During polymerization, the Mo / Bd molar ratio was 1.2×10 -3 . Polymerization was carried out according to the polymerization method of Example 1. The difference is that the polymerization is carried out at different temperatures, and the reaction time is 120h. According to the method of Example 1, the polybutadiene obtained in this example was characterized. The polymerization conditions and polymer test results are shown in Table 3.
[0045] Table 3 Temperature vs. AlEt 3 / MoCl 3 (OC 8 h 17 ) 2 Effect of Catalytic System on Obtained Polymer Structure
[0046] temperature Conversion rates% 1,2% Mn*10 4
[0047] The data in Table 3 shows that as long as sufficient time is given to the polymerization, low-te...
PUM
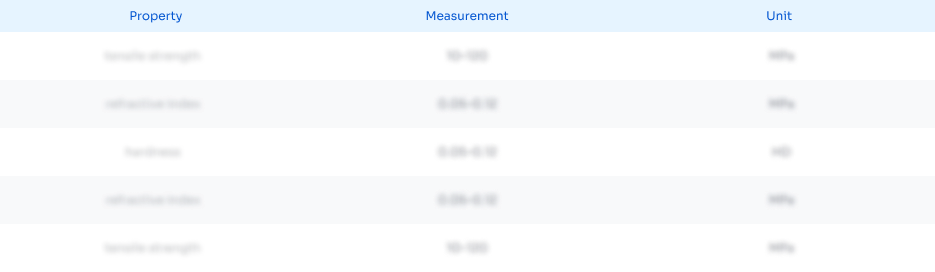
Abstract
Description
Claims
Application Information

- R&D Engineer
- R&D Manager
- IP Professional
- Industry Leading Data Capabilities
- Powerful AI technology
- Patent DNA Extraction
Browse by: Latest US Patents, China's latest patents, Technical Efficacy Thesaurus, Application Domain, Technology Topic, Popular Technical Reports.
© 2024 PatSnap. All rights reserved.Legal|Privacy policy|Modern Slavery Act Transparency Statement|Sitemap|About US| Contact US: help@patsnap.com