Spring grinding equipment
A grinding and equipment technology, used in grinding/polishing equipment, metal processing equipment, grinding machines, etc., can solve the problems of continuous operation, low processing efficiency, troublesome operation, etc., to improve processing efficiency, improve service life, structure simple effect
- Summary
- Abstract
- Description
- Claims
- Application Information
AI Technical Summary
Problems solved by technology
Method used
Image
Examples
Embodiment Construction
[0013] The present invention will be described in further detail below by means of specific embodiments:
[0014] The reference signs in the drawings of the description include: grinding disc 1, top disc 2, chassis 3, spring door 4, spring hole 5, notch 6, rotating shaft 7, inclined seam 8.
[0015] The embodiment is basically as attached figure 1 Shown: comprises rotating shaft 7, and top plate 2 and chassis 3 are connected to rotate on rotating shaft 7, and grinding disc 1 is installed between top disc 2 and chassis 3, and grinding disc 1 is connected with rotating shaft 7. There are spring holes 5 for holding springs on the grinding disc 1, and the spring holes 5 are evenly distributed on the grinding disc 1. Wear-resistant layers are installed on the two end faces of the spring holes 5; there is a 60-degree gap 6 on the top disc 2, which can be directly passed through The notch 6 of the top disc 2 sees the spring hole 5 on the grinding disc 1, the lower bottom surface of ...
PUM
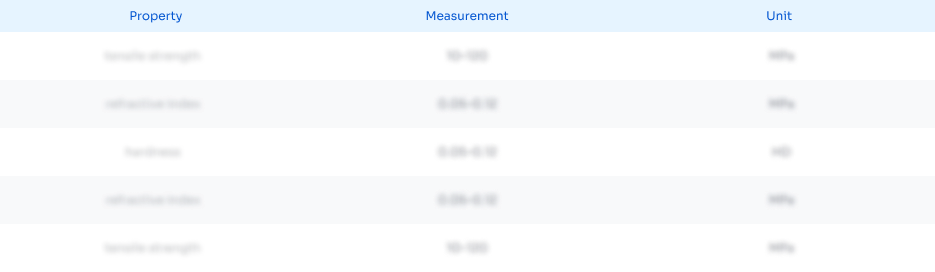
Abstract
Description
Claims
Application Information

- R&D Engineer
- R&D Manager
- IP Professional
- Industry Leading Data Capabilities
- Powerful AI technology
- Patent DNA Extraction
Browse by: Latest US Patents, China's latest patents, Technical Efficacy Thesaurus, Application Domain, Technology Topic, Popular Technical Reports.
© 2024 PatSnap. All rights reserved.Legal|Privacy policy|Modern Slavery Act Transparency Statement|Sitemap|About US| Contact US: help@patsnap.com