A Rectangular Smelting Section Feeding Process of Electron Beam Cooling Hearth Furnace for Titanium or Titanium Alloy
An electron beam cooling bed furnace and titanium alloy technology, which is applied in the field of rectangular melting section feeding of electron beam cooling bed furnaces, can solve the problems of decreased ingot yield, section cracking, riser and the like, and achieves convenient operation, simple process, Use good effect
- Summary
- Abstract
- Description
- Claims
- Application Information
AI Technical Summary
Problems solved by technology
Method used
Image
Examples
Embodiment 1
[0016] The electron beam cooling hearth furnace casting ingot rectangular smelting section feeding process for titanium or titanium alloy includes the following steps:
[0017] (1) Determine the feeding shrinkage section of the ingot cast in the electron beam cooling hearth furnace. Taking an ingot with a specification of 1050×210mm and the feeding position as the tail of the ingot as an example, the determination method is to define the head of the ingot within 100mm from the starting casting surface to the ingot length; when all the materials in the bucket are added to the electron beam After the smelting and cooling bed of the cooling bed furnace, confirm the position of the ingot length at this time, and define the casting length within 150mm from the end face of the tail as the tail of the ingot;
[0018] (2) Close the feeding system of the system and stop feeding. After all the materials are melted, observe the flow of the metal liquid at the overflow port on the smeltin...
Embodiment 2
[0025] The electron beam cooling hearth furnace casting ingot rectangular smelting section feeding process for titanium or titanium alloy includes the following steps:
[0026] (1) Determine the feeding shrinkage section of the ingot cast in the electron beam cooling hearth furnace. Taking the ingot with the specification of 1380×210mm and the feeding position as the head of the ingot as an example (sudden interruption of smelting, the ingot is connected through the feeding process) as an example, the determination method is to place the casting surface within 100mm of the ingot length Defined as the head of the ingot; when all the material in the bucket is added to the smelting and cooling bed of the electron beam cooling bed furnace, confirm the position of the ingot length at this time, and define the casting length within 150mm from the end face of the tail as the tail of the ingot;
[0027] (2) When the length of the head of the cast ingot is 80 mm, close the feeding syst...
PUM
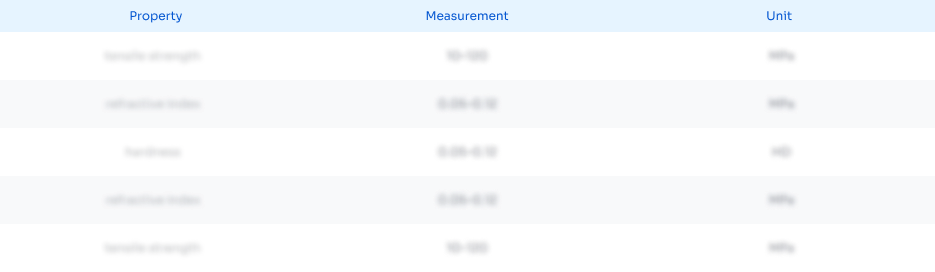
Abstract
Description
Claims
Application Information

- R&D Engineer
- R&D Manager
- IP Professional
- Industry Leading Data Capabilities
- Powerful AI technology
- Patent DNA Extraction
Browse by: Latest US Patents, China's latest patents, Technical Efficacy Thesaurus, Application Domain, Technology Topic, Popular Technical Reports.
© 2024 PatSnap. All rights reserved.Legal|Privacy policy|Modern Slavery Act Transparency Statement|Sitemap|About US| Contact US: help@patsnap.com