A kind of additive used in the raw material mixing process of ceramic friction material and its preparation method
A friction material and mixing process technology, which is applied in the additive and preparation field of ceramic friction material raw material mixing process, can solve the problems of poor slipping and friction performance, poor thermal stability, potential safety hazards, etc., and achieve improved surface activity and improved friction coefficient , prevent slippery effect
- Summary
- Abstract
- Description
- Claims
- Application Information
AI Technical Summary
Problems solved by technology
Method used
Image
Examples
Embodiment 1
[0025] An additive used in the mixing process of ceramic friction materials. The raw materials are 3kg ceramic loose cotton, 0.3kg carbon fiber, 0.1kg potassium titanate fiber, 1kg waste oil, 3kg diesel, 1kg paint, and 1kg coal powder. Among them, ceramic loose cotton is made by treating 10 parts by mass of clay clinker, 9 parts by mass of alumina powder, 5 parts by mass of silica powder, and 1 part by mass of chromite sand at a temperature of 300°C for 20 minutes, and then melting it in an electric furnace. , It is obtained by spinning it into fibrous silk with a spinning machine, and then collecting cotton with a cotton collector.
[0026] The method for preparing additives used in the mixing process of ceramic friction materials includes the following steps:
[0027] (1) The ceramic loose cotton is soaked in trench oil, and during the soaking process, one-third of coal powder is added to it, and the temperature is adjusted to 300℃, the vacuum degree is 0.02MPa, and the ultrasoni...
Embodiment 2
[0032] An additive used in the mixing process of ceramic friction materials. The raw material components are 7kg ceramic loose cotton, 0.9kg carbon fiber, 0.7kg potassium titanate fiber, 3kg waste oil, 7kg diesel, 3kg paint, and 7kg coal powder. Among them, ceramic loose cotton is made by treating 20 parts by mass of clay clinker, 11 parts by mass of alumina powder, 9 parts by mass of silica powder, and 3 parts by mass of chromite sand at a temperature of 500°C for 30 minutes, and then melting it in an electric furnace. , It is obtained by spinning it into fibrous silk with a spinning machine, and then collecting cotton with a cotton collector.
[0033] The specific preparation method of the ceramic loose cotton is to mix clay clinker, alumina powder, silica powder, and chromite sand, and then treat it at 500°C for 30 minutes, then ultrasonic treatment for 10 seconds, and then add it to it The clarified lime water, which accounts for 1% of the mixed material, is then sent to the ...
Embodiment 3
[0041] An additive used in the mixing process of ceramic friction materials. The raw material components are 5kg of ceramic loose cotton, 0.6kg of carbon fiber, 0.4kg of potassium titanate fiber, 2kg of waste oil, 5kg of diesel, 2kg of paint, and 3kg of coal powder. Among them, ceramic loose cotton is made by treating 15 parts by mass of clay clinker, 10 parts by mass of alumina powder, 7 parts by mass of silica powder, and 2 parts by mass of chromite sand at a temperature of 400°C for 25 minutes, and then melting it in an electric furnace. , It is obtained by spinning it into fibrous silk with a spinning machine, and then collecting cotton with a cotton collector.
[0042] The specific preparation method of the ceramic loose cotton is to mix clay clinker, alumina powder, silica powder, and chromite sand, and then treat it at 400°C for 25 minutes, and then ultrasonic treatment for 20 seconds, and then add it to it The clarified lime water, which accounts for 3% of the mixed mater...
PUM
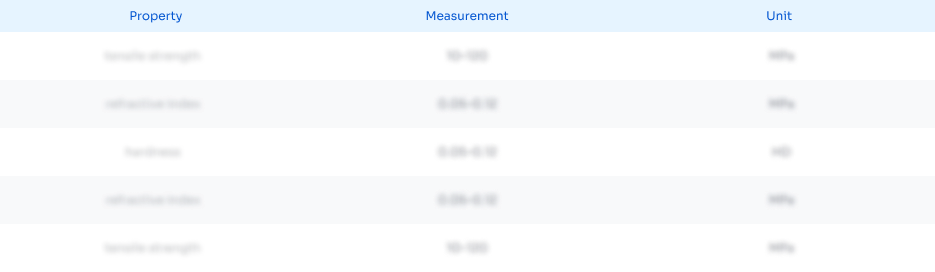
Abstract
Description
Claims
Application Information

- R&D
- Intellectual Property
- Life Sciences
- Materials
- Tech Scout
- Unparalleled Data Quality
- Higher Quality Content
- 60% Fewer Hallucinations
Browse by: Latest US Patents, China's latest patents, Technical Efficacy Thesaurus, Application Domain, Technology Topic, Popular Technical Reports.
© 2025 PatSnap. All rights reserved.Legal|Privacy policy|Modern Slavery Act Transparency Statement|Sitemap|About US| Contact US: help@patsnap.com