Hydraulic clamping device with powerful self-locking function
A hydraulic clamping and self-locking technology, used in clamping, workpiece clamping devices, supports, etc., can solve the problems of low bearing capacity, high strength and rigidity requirements, reduced clamping rigidity and precision, etc., to achieve convenient operation, Compact structure, self-locking and reliable effect
- Summary
- Abstract
- Description
- Claims
- Application Information
AI Technical Summary
Problems solved by technology
Method used
Image
Examples
Embodiment Construction
[0019] The specific implementation manner of the present invention will be described below in conjunction with the accompanying drawings.
[0020] Such as figure 1 , figure 2 with image 3 As shown, the powerful self-locking hydraulic clamp of this embodiment includes a base body 1, the front end of the base body 1 is provided with a cover body 11, and the upper and lower ends of the side wall of the base body 1 are respectively provided with guiding square holes, which are located in the base body. An oil cylinder 2 is suspended inside the body 1, and a symmetrical piston rod 3 protrudes from the upper and lower ends of the oil cylinder 2 respectively. The head of the piston rod 3 is connected to the front connecting rod 4 and the rear connecting rod 13 through the piston rod pin 14. The rear connecting rod 13 The other end is connected to the hinge seat on the inner wall of the seat body 1 through the hinge pin 12, and the other end of the front connecting rod 4 is connec...
PUM
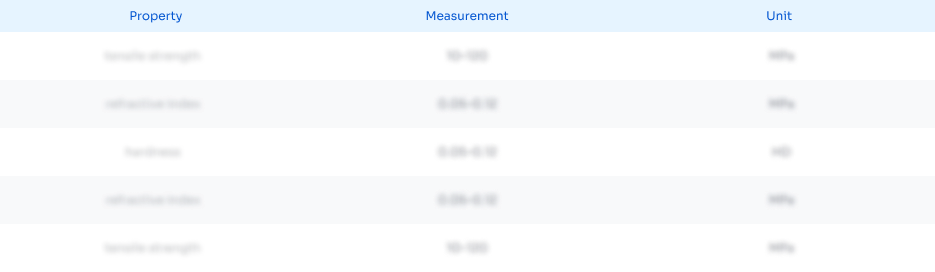
Abstract
Description
Claims
Application Information

- Generate Ideas
- Intellectual Property
- Life Sciences
- Materials
- Tech Scout
- Unparalleled Data Quality
- Higher Quality Content
- 60% Fewer Hallucinations
Browse by: Latest US Patents, China's latest patents, Technical Efficacy Thesaurus, Application Domain, Technology Topic, Popular Technical Reports.
© 2025 PatSnap. All rights reserved.Legal|Privacy policy|Modern Slavery Act Transparency Statement|Sitemap|About US| Contact US: help@patsnap.com