High-strength towing-used photoelectric composite cable and manufacture method thereof
A technology of photoelectric composite cable and manufacturing method, which is applied in the direction of cable/conductor manufacturing, insulated cable, power cable with shielding layer/conductive layer, etc., and can solve compatibility, low temperature resistance, compression set resistance, thermal aging Reduced performance, inapplicability of chlorinated polyethylene, low tear resistance and other problems, to achieve the effect of improved tear strength, good physical and mechanical properties, and simple preparation process
- Summary
- Abstract
- Description
- Claims
- Application Information
AI Technical Summary
Problems solved by technology
Method used
Image
Examples
Embodiment 1
[0050] Embodiment 1: A photoelectric composite cable for high-strength towing, the photoelectric composite cable includes a photoelectric unit 1, a ground core conductor 2 and at least three power core conductors 3, and the outer surface of the power core conductor 3 is Covered with a first semiconductive shielding layer 4, an ethylene-propylene rubber layer 5 and a second semiconductive shielding layer 6 in sequence, the outer surface of the ground core conductor 2 is covered with a semiconductive rubber layer 7, and the photoelectric unit 1 is further Including a loose tube 8 and a tensile insulating layer 9, the loose tube 8 is filled with several optical fibers 10;
[0051] The special neoprene inner sheath 11 is coated on the outer surface of the photoelectric unit 1, at least two ground core conductors 2 and at least three power core conductors 3, and the outer sheath 12 is coated on the special neoprene inner sheath. The outer surface of the sleeve 11, the special neopr...
Embodiment 2
[0063] Embodiment 2: A photoelectric composite cable for high-strength towing. The photoelectric composite cable includes a photoelectric unit 1, a ground core conductor 2 and at least three power core conductors 3. The outer surface of the power core conductor 3 is Covered with a first semiconductive shielding layer 4, an ethylene-propylene rubber layer 5 and a second semiconductive shielding layer 6 in sequence, the outer surface of the ground core conductor 2 is covered with a semiconductive rubber layer 7, and the photoelectric unit 1 is further Including a loose tube 8 and a tensile insulating layer 9, the loose tube 8 is filled with several optical fibers 10;
[0064] The special neoprene inner sheath 11 is coated on the outer surface of the photoelectric unit 1, at least two ground core conductors 2 and at least three power core conductors 3, and the outer sheath 12 is coated on the special neoprene inner sheath. The outer surface of the sleeve 11, the special neoprene ...
Embodiment 3
[0070] Embodiment 3: A photoelectric composite cable for high-strength towing. The photoelectric composite cable includes a photoelectric unit 1, a ground core conductor 2 and at least three power core conductors 3. The outer surface of the power core conductor 3 is Covered with a first semiconductive shielding layer 4, an ethylene-propylene rubber layer 5 and a second semiconductive shielding layer 6 in sequence, the outer surface of the ground core conductor 2 is covered with a semiconductive rubber layer 7, and the photoelectric unit 1 is further Including a loose tube 8 and a tensile insulating layer 9, the loose tube 8 is filled with several optical fibers 10;
[0071] The special neoprene inner sheath 11 is coated on the outer surface of the photoelectric unit 1, at least two ground core conductors 2 and at least three power core conductors 3, and the outer sheath 12 is coated on the special neoprene inner sheath. The outer surface of the sleeve 11, the special neoprene ...
PUM
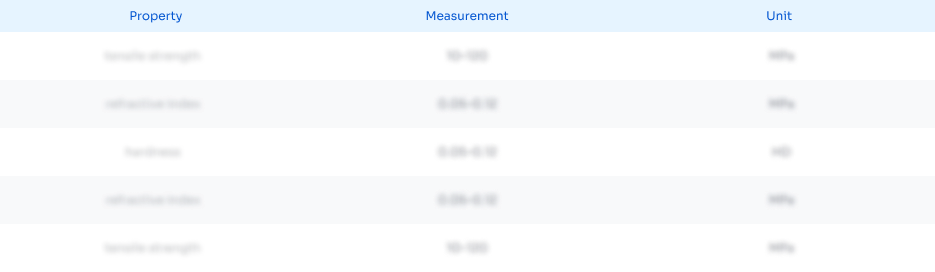
Abstract
Description
Claims
Application Information

- Generate Ideas
- Intellectual Property
- Life Sciences
- Materials
- Tech Scout
- Unparalleled Data Quality
- Higher Quality Content
- 60% Fewer Hallucinations
Browse by: Latest US Patents, China's latest patents, Technical Efficacy Thesaurus, Application Domain, Technology Topic, Popular Technical Reports.
© 2025 PatSnap. All rights reserved.Legal|Privacy policy|Modern Slavery Act Transparency Statement|Sitemap|About US| Contact US: help@patsnap.com