A kind of phenolic resin black functional masterbatch and preparation method thereof
A technology of phenolic resin and functional masterbatch, which is applied in the field of phenolic resin black functional masterbatch and its preparation, can solve the problems of affecting the curing speed of phenolic resin, limitation of carbon black dispersion and utilization, easy pollution of production links, etc., so as to improve the dyeing ability , The heat distortion temperature is increased, and the fluidity is good.
- Summary
- Abstract
- Description
- Claims
- Application Information
AI Technical Summary
Problems solved by technology
Method used
Image
Examples
Embodiment 1
[0033] A phenolic resin black functional masterbatch of type F081-A was prepared. It is prepared from the following raw materials in parts by weight: 0.1 part of nano-calcium carbonate, 0.3 part of nano-montmorillonite, 6 parts of pigment carbon black, 0.1 part of dispersant, 0.1 part of lubricant, 0.01 part of defoamer, and 0.2 part of emulsifier part, 0.2 part of coupling agent.
[0034] The preparation method of the phenolic resin black functional masterbatch of model F081-A, carry out as follows:
[0035] Step 1: Pre-dispersion
[0036] Put nano-calcium carbonate and nano-montmorillonite in a high-speed mixer; add dispersant, lubricant, and stir at high speed for 1-3 minutes; then add coupling agent and continue stirring for 1-2 minutes; then add pigment carbon black , continue to stir for 5 to 8 minutes, and keep the temperature at 25°C to 45°C.
[0037] Step 2: Ball Mill Dispersion or Ultrasonic Dispersion
[0038] Put the material obtained in step 1 into a ball mill...
Embodiment 2
[0042]A phenolic resin black functional masterbatch of type F082-A was prepared. It is prepared from the following raw materials in parts by weight: 0.1 part of nano-montmorillonite, 0.4 part of nano-silica, 8 parts of pigment carbon black, 0.1 part of dispersant, 0.15 part of lubricant, 0.01 part of defoamer, emulsifier 0.1 part, 0.2 part of coupling agent.
[0043] The preparation method of the phenolic resin black functional masterbatch of model F082-A, carry out as follows:
[0044] Step 1: Pre-dispersion
[0045] Put nano-montmorillonite and nano-silica in a high-speed mixer; add dispersant, lubricant, and stir at high speed for 1-3 minutes; then add coupling agent and continue stirring for 1-2 minutes; then add pigment carbon black, continue stirring for 5-8 minutes, and keep the temperature at 25°C-45°C.
[0046] Step 2: Ball Mill Dispersion or Ultrasonic Dispersion
[0047] Put the material obtained in step 1 into a ball mill or ultrasonic dispersion equipment for ...
Embodiment 1-1
[0051] Embodiment 1-1 F081 type phenolic resin black functional masterbatch
[0052] The specific steps of preparation are as follows: In a 500mL three-necked flask equipped with a stirrer, a condenser, and a thermometer, first add 200g of molten phenol, and then add 148g of formaldehyde according to the molar ratio of phenol to formaldehyde of 1:0.74, start stirring, and heat to make the reaction The temperature of the system is controlled at 100 ℃ -104 ℃ for reaction, and when the liquid is observed to reflux, 2g-10g of catalyst is added according to the condition of 1%-5% of the mass of phenol. The catalyst is inorganic acid or organic acid, i.e. hydrochloric acid, sulfuric acid or oxalic acid, continue to react for 1h-2h, when the liquid is observed to be turbid, add 4g-10g of composite functional black dye F081-A emulsion according to the proportion, and reflux for 1.5h-2h , start dehydration under reduced pressure, and when the resin reaches a certain viscosity (10-15Pa·...
PUM
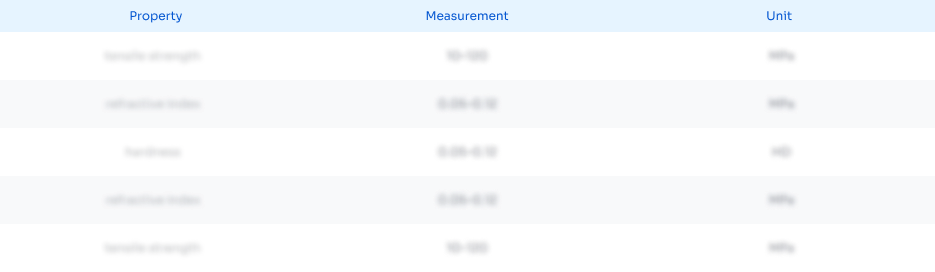
Abstract
Description
Claims
Application Information

- R&D
- Intellectual Property
- Life Sciences
- Materials
- Tech Scout
- Unparalleled Data Quality
- Higher Quality Content
- 60% Fewer Hallucinations
Browse by: Latest US Patents, China's latest patents, Technical Efficacy Thesaurus, Application Domain, Technology Topic, Popular Technical Reports.
© 2025 PatSnap. All rights reserved.Legal|Privacy policy|Modern Slavery Act Transparency Statement|Sitemap|About US| Contact US: help@patsnap.com