Stamping molding die for automobile front beam tube
An automobile front beam and stamping forming technology, applied in the field of stamping dies, can solve the problems of long working hours and high processing costs, and achieve the effects of preventing deformation, facilitating processing and small deformation.
- Summary
- Abstract
- Description
- Claims
- Application Information
AI Technical Summary
Problems solved by technology
Method used
Image
Examples
Embodiment Construction
[0020] Specific embodiments of the present invention will be described in detail below in conjunction with the accompanying drawings.
[0021] Such as Figure 2-6 As shown, a stamping mold for the front beam tube of an automobile comprises an upper die base 1 and a lower die base 2, the upper die base 1 is provided with an upper forming die assembly, and the lower die base 2 is provided with a lower forming die assembly , Mandrel components 3 are respectively provided at both ends of the lower molding component on the lower mold base 2 .
[0022] The upper molding die assembly includes upper end modules 4 which can move up and down at both ends and an upper middle module which is fixedly arranged on the upper mold base 1. The upper end modules 4 and the upper middle modules are provided with corresponding upper molding grooves. A nitrogen gas spring 6 is arranged between the upper end module 4 and the upper mold base 1. The movement stroke of the upper end module 4 is the dis...
PUM
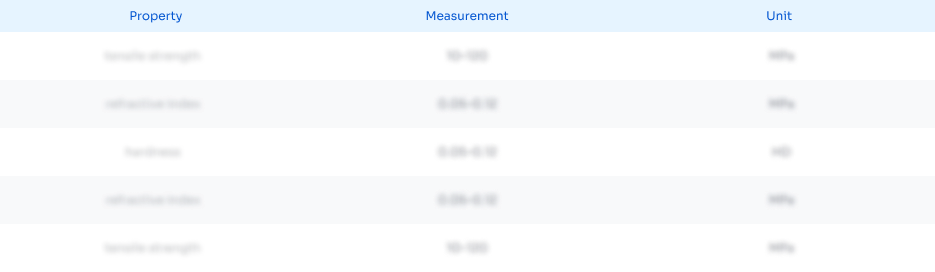
Abstract
Description
Claims
Application Information

- Generate Ideas
- Intellectual Property
- Life Sciences
- Materials
- Tech Scout
- Unparalleled Data Quality
- Higher Quality Content
- 60% Fewer Hallucinations
Browse by: Latest US Patents, China's latest patents, Technical Efficacy Thesaurus, Application Domain, Technology Topic, Popular Technical Reports.
© 2025 PatSnap. All rights reserved.Legal|Privacy policy|Modern Slavery Act Transparency Statement|Sitemap|About US| Contact US: help@patsnap.com