Manufacturing method of array substrate
A manufacturing method and array substrate technology, applied in the direction of electrical components, electrical solid devices, circuits, etc., can solve the problems of TET characteristic changes, pollution, and affecting the display effect of the display, and achieve the effect of guaranteeing the characteristics
- Summary
- Abstract
- Description
- Claims
- Application Information
AI Technical Summary
Problems solved by technology
Method used
Image
Examples
Embodiment Construction
[0044] The present invention will be described in detail below in conjunction with the accompanying drawings and specific embodiments.
[0045] refer to Figure 7 , is a schematic flowchart of a first embodiment of a method for fabricating an array substrate according to the present invention.
[0046] A method for manufacturing an array substrate provided by the present invention, the method includes the following steps:
[0047] S100, forming a gate metal structure 200 on the substrate 100, such as Figure 8 shown.
[0048] Wherein, the substrate 100 may be quartz glass, common glass, plastic substrate and so on. The gate metal structure 200 is a metal film deposited by physical sputtering, the metal film at least includes a Mo layer and a Cu layer, wherein the thickness of the Mo layer is 100A-300A, for example, 150A, 200A or 250A. The thickness of the Cu layer is about 3000A-6000A, such as 3500A, 4000A or 5000A. Alternatively, the metal film may also include a metal Ti ...
PUM
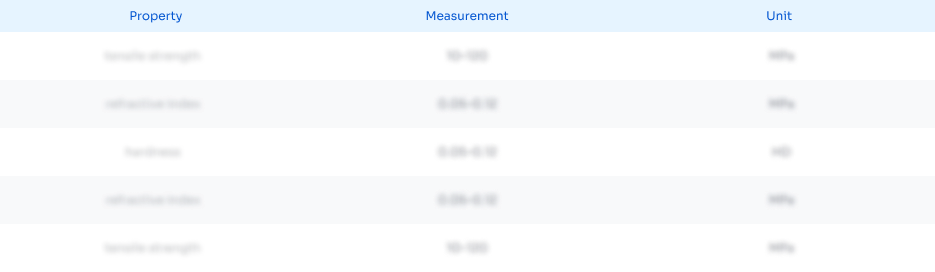
Abstract
Description
Claims
Application Information

- R&D Engineer
- R&D Manager
- IP Professional
- Industry Leading Data Capabilities
- Powerful AI technology
- Patent DNA Extraction
Browse by: Latest US Patents, China's latest patents, Technical Efficacy Thesaurus, Application Domain, Technology Topic, Popular Technical Reports.
© 2024 PatSnap. All rights reserved.Legal|Privacy policy|Modern Slavery Act Transparency Statement|Sitemap|About US| Contact US: help@patsnap.com