Electroslag re-melting process for controlling aluminum uniformity of high-aluminum steel
A technology of electroslag remelting and aluminum elements, which is applied in the field of electroslag metallurgy, can solve the problems of composition segregation, large differences in aluminum composition, and unsatisfactory effects, and achieve low cost and reduce the cost of electroslag production
- Summary
- Abstract
- Description
- Claims
- Application Information
AI Technical Summary
Problems solved by technology
Method used
Image
Examples
Embodiment Construction
[0014] An electroslag remelting process to control the uniformity of aluminum elements in high-aluminum steel, using NAK80 steel grade, ingot size: 5 tons; slag system: 56%CaF 2 +24%Al 2 o 3 +20% return slag of the same steel type (returned slag of the same steel type can be reused no more than 2 times); slag amount: 170kg. The slag material was baked at 600°C for 4 hours to remove moisture before slag melting. The consumable electrode is Φ500mm die-cast billet, and the average electroslag melting rate is controlled at 520~560kg / h. Add aluminum powder as a deoxidizer during remelting. According to the aluminum content of the electrode billet, add 80g / 5 minutes of aluminum powder within two hours before remelting, and then add 35g / 5 minutes. The remelting process uses an automatic feeder for deoxidation. After lifting the mold, observe that the surface quality of the electroslag ingot is good, and there are no pits and slag grooves on the surface. Electroslag remelting is c...
PUM
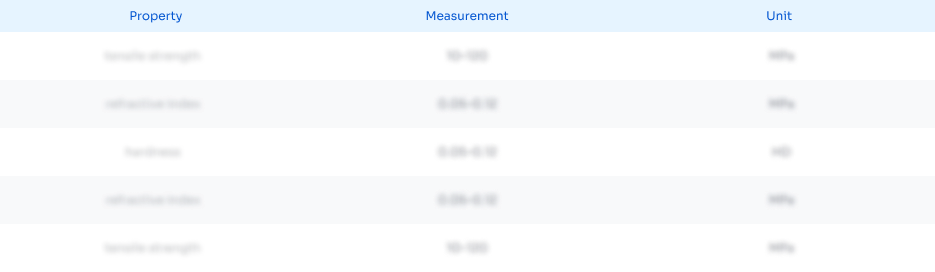
Abstract
Description
Claims
Application Information

- Generate Ideas
- Intellectual Property
- Life Sciences
- Materials
- Tech Scout
- Unparalleled Data Quality
- Higher Quality Content
- 60% Fewer Hallucinations
Browse by: Latest US Patents, China's latest patents, Technical Efficacy Thesaurus, Application Domain, Technology Topic, Popular Technical Reports.
© 2025 PatSnap. All rights reserved.Legal|Privacy policy|Modern Slavery Act Transparency Statement|Sitemap|About US| Contact US: help@patsnap.com